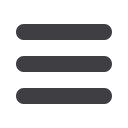

48
J
uly
2011
www.read-tpt.com›
T
echnology
U
pdate
AGENTS
REQUIRED
H1 and H2 tube piercing are applications
in which the holes being punched are
dimpled only. Unlike the punching method,
piercing does not use an internal mandrel
and die sections to keep the tube from
dimpling, but instead it uses external
guides to encapsulate the tube. This keeps
the OD of the tube consistent while the
punch pierces into the hollow tube drawing
material around it and forming a dimple.
H1 refers to a dimpled hole on one side,
while H2 refers to a dimpled hole on both
sides, or what is commonly referred to as
a double dimple.
Multicyl provides a standard system for
both H1 and H2 applications for tubes up to
1.5" diameter, and custom systems for larger
tubes. An H1 system is easily converted to
an H2 system by adding a punch assembly
to the bottom guide in the standard tool set.
H3 tube piercing refers to applications in
which the tube is pierced straight through
with one punch. Although classed as a
piercing application, it is actually a hybrid
between piercing and punching, as the top
side is pierced as described above in the
H1 and H2 section, but the bottom hole is
actually punched from the inside out as the
punch travels through to the bottom of the
tube and punches the bottom hole against
an external die.
Multicyl straight through tube pierce
stations produce a through hole that is
dimpled on the top and clean on the
bottom. Maintenance may be higher
with this application, as the punch tip is
significantly longer and the bottom hole
is actually punched with the slug from the
top hole.
Multicyl Inc
– Canada
Fax: +1 905 951 0672
Email:
sales@multicyl.comWebsite:
www.multicyl.com12" and
16" five roll
welding
stands
THE new large size mill welding stand from
Oto Mills is designed to integrate rigidity,
simplicity, quick roll changeover and
easiness of roll setting. The configuration
is a typical five roll weld stand: Nr 2
squeeze rolls, Nr 2 top inclined rolls and
Nr 1 bottom support roll.
For small tubes the welding stand can be
fitted with only four rolls (two squeeze and two
top), while the bottom roll is cylindrical and
used as vertical support for the squeeze rolls.
Special features include slide guide of
squeeze rolls located on the back of squeeze
rolls to avoid contamination/accumulation of
weld spume and projected particles; quick
changeover cassettes – top and squeeze
rolls are assembled in cassettes for quick
changeover; and simplified roll changeover
with top tilting frame.
The top frame tilts back by hydraulic
cylinders to leave space for replacing the
squeeze rolls with an overhead crane. The
hydraulic locking cylinders guarantee a
strong and rigid configuration.
The design has been optimised with
special consideration of the welding induction
process, in order to maximise the efficiency
of energy transfer from coil to the edges to
be welded. The back of frame is designed to
allow easy access to the inside scarfing unit,
for insert replacement.
The main features for adjustments are:
adjustment of squeeze rolls with AC gear
motors and absolute encoder/transducer;
vertical adjustment of bottom roll with AC
gear motors and absolute encoder/transducer;
separate vertical adjustment of top rolls with
AC gear motors and absolute encoder/
transducer; simultaneous self centring
transversal adjustment (to suit width of weld
bead) with AC gear motors; simultaneous
transversal adjustment for alignment of top rolls
across mill centreline with AC gear motors; top
frame of squeeze box is tiltable downstream
for squeeze roll replacement; tilting cylinder
and hydraulic locks in working position fitted to
the bottom squeeze box frame; rolls shall be
supplied completely assembled with shafts,
bearings and seals; and top roll forks with
quick changeover system.
A similar design is used on the smaller
12" size with hydraulic motors and absolute
encoder as option.
Oto Mills SpA
– Italy
Fax: +39 0522 964188
Website:
www.otomills.comH1, H2 and H3 tube piercing