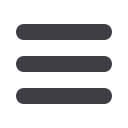

Technology News
www.read-tpt.com24
N
ovember
2015
Continuous casting
technology
UPCAST OY is a supplier of Upcast
®
-
SGTube production lines for upward
casting of thin-walled Cu-DHP tubes
ready for further processing into various
high quality tube products.
Upcast-SGTube continuous casting
technology offers a shortcut in copper
tube production process, using one step
compared to the traditional multi-step
tube production. It is an extension of the
Upcast system used for casting Cu and
Cu-alloy rod, sharing the same benefits
of the standard system, with specific
construction of the casting machine,
coilers and casting machine tooling.
The Upcast-SG cast tube has a
fine grain structure allowing for its
straight breakdown drawing followed
by inductive in-line annealing. To
ensure complete softening a total area
reduction of min 50 per cent is required
before intermediate annealing.
Upcast rod and Upcast-SGTube
lines are both of modular design,
offering solutions for small and medium
capacities. With a double-furnace
configuration (separate melting and
casting furnaces) it is possible to reach
12,000 tpa. Sizes of tube with outer
diameters from 38 to 60mm have been
cast, with wall thicknesses of 2mm and
3mm respectively.
Different tube sizes can be cast
simultaneously when the casting
machine is equipped with more than
one servo-drive system. The smaller the
final tube size, the smaller the cast tube
size. With respect to coil weight, Upcast-
SGTube is flexible, with an upper limit
of around 1.5 tons. The final weight limit
is more likely to be determined by the
downstream process equipment.
The main use of Upcast-SGTube is
in the casting of phosphor deoxidised
(DHP) copper tube for the production of
sanitary, industrial and ACR tubing. The
process is not limited to DHP copper,
and is also suitable for other copper
grades/copper alloys. Oxygen-free
copper and copper nickel alloys have all
been successfully cast.
Having the Upcast-SGTube process
as the first step of tube production is
claimed to reduce energy consumption.
It is also possible to use clean and dry
scrap in the process with the double-
furnace configuration.
Upcast OY
– Finland
Fax: +358 207 577 401
Email:
upcast@upcast.comWebsite:
www.upcast.comDouble-furnace
configuration
SG cast tube in a coil
Bendcheck assures straightness
ABSOLUTE straightness is one of the
most important criteria in the production
of round bars and pipes. Bendcheck –
the precision laser measuring system
from Zumbach – monitors bending
continuously without missing any
sections directly within the production
process.
This replaces the ODAC
®
laser
measuring heads used currently to
manually spot test with a non-contact
online test for bending. Apart from the
obvious gain in quality the manufacturer
also saves considerable time through
the use of the online data check.
Bendcheck can be used for:
synchronous real time scanning in the
production process; quality assurance
directly after the straightening process;
direct integration in the production
process (customer-specific installation);
and no time consuming and laborious
checks with manual tools.
The system measures the position
and diameter of the product at three
different locations along its axis.
Bendcheck calculates the deviation of
the central measuring head in respect of
a virtual straight line projected from the
position of the left head to the position
of the right head, from the data. This
value is either divided by the distance or
by the distance squared. The operator
can select the preferred formula for
the bend calculation. Thanks to this
information, the bend of the product is
continuously calculated and graphically
displayed. Bendcheck can be operated
in a continuous measuring mode without
encoder, or in a triggered mode where
the measurement pulse is generated by
an encoder along the cutting edge.
The respective data is clearly shown
on a display board. Diameter, absolute
bend value, bending angle as well as the
individual and current measurements
of the three measuring heads are
clearly shown. Additional statistics
complement the informative value of the
measurement.
Zumbach Electronic AG
– Switzerland
Email:
sales@zumbach.chWebsite:
www.zumbach.com