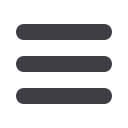

Technology News
www.read-tpt.com32
N
ovember
2015
Long life in aggressive solutions
E BRAUDE is based in the UK and has
been serving industry for more than 58
years. Traditionally it has been focused
on the liquids and conditions other
suppliers avoid, and its expertise is
in aggressive and corrosive solutions
that conventional equipment cannot
withstand.
Braude has been exporting for many
years, and has recently increased its
efforts in the Asian markets. One of the
company’s strengths is the ability to
tailor products to suit customers’ specific
needs. Braude was recently approached
by a company in India building a plant
for a stainless steel tube manufacturer,
which required an offline heating system
in a new pickling facility.
The heat exchanger had a high output
of 400,000kcal/hr on a saturated steam
system. Braude designed and built
steam heat exchangers specifically
to suit the tanks, while meeting the
challenges of the cost profile.
Braude also recently undertook
another contract in Asia to supply heat
exchangers for the pre-treatment line for
one of the largest galvanising plants in
the world.
All of Braude’s products are
manufactured from high integrity
chemically inert fluoropolymers (eg
Teflon™), and are designed to ensure
long life in aggressive solutions.
The product range includes tank
and vessel heaters/coolers for use
with steam, hot water or thermal fluids;
chemical service pumps; external
heating systems that are mounted
outside the process tank to avoid
clutter and to prevent damage by heavy
workloads; and electric heaters and
controllers.
E Braude (London) Ltd
– UK
Fax: +44 1252 875281
Email:
sales@braude.co.ukWebsite:
www.braude.co.ukTest run proves decisive
PRECISION stampings require not only
cutting-edge press and die technology,
but also high-performance levellers:
several rollers straighten the sheet
metal as it leaves the coil and eliminate
any defects – such as cross bows
which cannot be completely avoided in
production – with the aid of an alternate
bending process.
The specific requirements for an
optimum straightening process are
defined by the material and finished
component. In order to find the right
machine, SKA and Schuler precisely
defined which materials would be used
in production for which end products.
“Until the end of the 1990s we used
levellers with nine rollers, as we used to
produce guide rails from relatively soft
materials,” recalled Guido Schneider,
SKA’s chief technology officer. However,
the requirements regarding materials
and tolerances for part quality have
grown steadily over the years, and this
necessitated the use of classic multi-
roller levellers. However, even these
machines were not completely suitable
for the targeted production portfolio.
Schuler then offered to run tests with
different strips of material on a leveller
for one day, in addition to providing on-
site expertise. “It turned out that the
number of rollers was not the decisive
factor,” reported Mr Schneider. “In fact, a
17-roller machine with significantly higher
rigidity was the better choice for us.”
One year later, in June 2014, the fine
levelling machine was finally put into
operation upstream of a 400-metric-ton
press supplied by Schuler – one of seven
at SKA. The overall system not only
increased output and part quality, but
even decreased energy consumption.
“The line has since been running
without any downtime and has not
given us any problems,” said Mr
Schneider. “Looking back, I have to
say that the test day was the decisive
factor for us. Schuler proved that the
fine leveller could straighten cross
bows in exactly the quality we need. In
the past, we often had to readjust the
die on a press because the material
properties changed within a few
metres. Obviously, this also depends
on the quality of the coil, but the
Schuler device can generally balance
out fluctuations so well that nothing is
noticed in the die or product. I would
definitely work together with Schuler
again.”
Schuler AG
– Germany
Fax: +49 7161 66 907
Website:
www.schulergroup.comWith just 17 rollers, the rigid machine
balances out fluctuations in the coil stock
Photo credit: Schuler
SKA’s fine levelling machine is positioned upstream of a 400t press, also supplied by Schuler