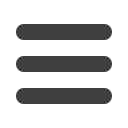

55
www.read-wca.comWire & Cable ASIA – July/August 2016
2.2 Spark Tester
A spark tester is equipment that can be used to detect
pinhole-type defects. The machine creates a spark when
there is a pinhole that exposes the core of the cable –
conductive metal. However, if a pinhole does not expose
the core, the spark is not created. But the pinhole that
is not a through hole is still a defect since over time the
pinhole could expand and expose the core of the cable.
Also, for products without a core (pipe, hose, tubing) or
products without a conducting core (fibre optic cable),
spark testers are not applicable.
2.3 Vision Systems
Prior configurations of surface defect detection systems
were unable to identify and measure convolutions of
the product. These systems were limited to ignoring
the convolutions to identify significant defects such as
pinholes or significant bulges or shape changes. The wrap
inspection system has been improved with additional
image processing software and alternative camera
configurations that identifies the wrapped cable profile
and can measure parameters and detect variations in the
wrapping that are considered defects.
3 Machine Vision Inspection System
3.1 Optical Mechanical Design
The wrap defect inspection system consists of one or
more high resolution cameras and adequate lighting
to capture images of cable moving at speeds more
than 1,200 feet (400 metres) per minute. Using multiple
cameras, 360-degree coverage of the cable surface can
be achieved. The system produces high quality images at
these speeds with a very high frame rate. The frame rate
is synchronised with an encoder and speed algorithm. The
lighting varies depending on the application.
The factors in consideration are the reflectivity of the
material, surface profile, colour, line speed and camera
type.
To ensure consistency in the images, the setup features an
enclosure to prevent ambient lighting, outside particles,
etc from affecting the results. Vibration of the cable is
minimised by cable guides, preventing images from being
out of focus.
An advanced algorithm is used to process the images
for cable wrap inspection. A typical algorithm is capable
of detecting surface and wrapping defects such as
scratches, holes, uneven wrapping, incorrect wrapping
angle, tape peeling and tape tears. The algorithm requires
analysis of the pixels of the image and grouping them for
further interpretation. If a defect is detected, an alarm
will notify the operator and an error report is saved to the
on-going data log. The defect will also show up on the
display for operators to clarify.
3.2 Improving Quality Assurance
Suitable for any type of products
: Since the surface defect
detection system with accurate diameter measurement
uses machine vision, it can be used to inspect the surface
for many types of wrapped products or convoluted
profiles.
It is the most thorough method of detecting wrapping and
surface flaws available and the advanced algorithm can
help classify the type of defects accordingly.
❍
❍
Figure 1
:
Uneven wrapping
❍
❍
Figure 2
:
Surface blemishes
❍
❍
Figure 3
:
Tape peeling
❍
❍
Figure 4
:
Tape wrinkle
❍
❍
Figure 5
:
Armour puckering
❍
❍
Figure 6
:
Discolouration