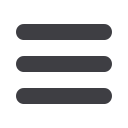

36
¦
MechChem Africa
•
June 2017
⎪
Products and industry news
⎪
Cable reeling solutions like no other from Powermite
Cable reeling systems are used to lay down
and retrieve cable in applications where a
predetermined length of travel and a fixed
amount of cable is connected to a fixed point
while amoving point travels over a fixed line,
rail, ground or height at a set speed.
The materials handling division of me-
chanical andelectrical engineering specialist,
Powermite, a division of Hudaco, supplies
superior quality, rugged, reliable, and eco-
nomical cable reeling systems and accesso-
ries to a wide spectrum of Southern African
industries, including medium voltage, low
voltage andmilli-power, control, fibre optic/
data and composite cables, and more.
“Ourcablereelingsystemsdelivernumer-
ous cost- and time-saving benefits for end-
users,” says Powermite marketing director,
DonovanMarks.“Theirextremelyruggedde-
signensures reliableoperation for optimised
uptime and productivity. Manufactured
in a variety of materials including painted
steel, stainless steel and hot dip galvanized
surfaces, the cable reeling equipment is suit-
able for a wide range of indoor and outdoor
applications.”
By utilising the anti-runback bearing/
braking resistive-based drive systems,
Powermite achieves tremendous success
with systemreliability. “Our systems contin-
ue tooperateover several years inextremely
dusty and corrosive environments.
“In addition, the greased-for-lifebearings
ensure a maintenance-free cable reeling
solution. With no stoppages for mainte-
nance and nomaintenance costs, our reeling
systems deliver significant cost savings for
end-users,” notes Marks.
These systems are also extremely ver-
satile and can be applied to low speeds
(5 m/min) or high speeds (120 m/min) over
distances ranging from1mto over a 1 000m
and the lengthcanbe increasedor decreased
to meet end-users’ requirements.
Powermitedrives are supplementedwith
VariableSpeedDrive (VSD) technology. “Our
VSD technology enables all the drives to
provide a constant torque to keep the cor-
rect tension at all times which is crucial to
preventing damage by protecting the cable
andkeeping it out of harm’swayduringwind-
ing and un-winding functions.”
www.powermite.co.zaThe recent introduction of SMC’s new
valves in the AS-R and AS-Q series, high-
lights the automation specialist’s com-
mitment to energy savings. Customers
achieve a cut in internal air consumption
by up to 25% when using the AS-R pres-
sure valve and anAS-Qflowvalve on their
cylinders.
Productmanager for SMCPneumatics,
Brian Abbott, explains some benefits of
using these valves in applications, for
example that the use of these valves helps
shorten the response time of the return
stroke andharmonises strokemovements
to prevent a harsh jerky start.
In pressing applications, these valves
enable a rapid supply of compressed air
at the end of the stroke, and the valve
bodies and plug-and-socket connections
Valve reduces air consumption by up to 40%
Powermite’s rugged cable reeling systems deliver
reliable operation for optimised uptime and
productivity.
can rotate 360° to ensure fast and easy
installation, he says.
SMC’s range of pressure and flow
valves includes six AS-R and five AS-Q
models: R1/8, R1/4, R3/8 and R1/2 con-
nection sizes and for hose diameters
ranging from 6 to 12 mm.
“Customers are able to choose be-
tween the new AS-R series with its fixed
2 bar supply pressure and the older ASR
valveswith fixed or variable set pressures
depending on the applicationwhere pres-
sures areadjustedmanuallyusingahandle
with a three-part scale,” explains Abbott.
The pressure valve and flow valve is
mounted together on cylinders. TheAS-Q
SMC’s AS-R and AS-Q
valves cut internal air
consumption by up
to 25% when used on
cylinders.
In response to ongoing changes in South
Africa’s heavy engineering industry, the
DCD Group is consolidating aspects of
its manufacturing capacity and expertise
into its Gravico Heavy Engineering joint
venture.AccordingtoDCDchiefexecutive
officerDigbyGlover, themovecomes after
detailedmarket studies and follows years
of depressed market conditions.
Louw Kriel, managing director of
Gravico, adds: “The manufacturing in-
dustry is changing andmanufacturers are
re-evaluating and developing new ways
to do business. Gravico’s strategy for the
flow valve is installed on the working
stroke side and the AS-R pressure valve
on the return stroke side. “The two valve
series have similar designs: the pressure
valves consist of regulator, with a check
valve and a throttle check valve. The
flow valves in the AS-Q series contain a
quick supply valve, an exhaust valve and
a throttle check valve.”
AS-R/AS-Q valves are recommended
for cylinders with a diameter of 32 mm
up to 125 mm bore, and an inlet pressure
of at least 3 bar, whichmeans that savings
actually increase with bigger cylinders or
higher air consumption levels and larger
pressuredifferencesbetween theworking
and return strokes.
www.smcpneumatics.co.zaGravico’s strategy for the new economy
new economy is focused on developing
and applying value-adding technologies,
rather than relyingonamarket upswingor
short-term cost containment measures.”
“Gravico is instituting a long-termcost
management and operational improve-
ment culture by investing in technology,”
Kriel says. “Wewill offer our ownproducts
instead of just manufacturing capacity,
and will concentrate on the expansion of
sales territories andcoverage.Wewill also
prospect andexploitnewmarketnicheson
a continuous basis,” he reveals.
www.dcd.co.za