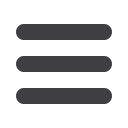

Furnaces
and
heat treatment
www.read-tpt.com88
M
arch
2013
Furnace rollers from the Ukraine
RESEARCH & Production Corporation
Trubostal Ltd was created in 1989,
and currently numbers more than
1,000 employees and two factories.
Total working area is 46,000m
2
. The
company’s plant for production of
centrifugally cast tubes and items is
described as the largest in Europe in
regard to that type of product.
Production capacity of liquid metal
is greater than 20,000 tons per year:
seamless centrifugally cast tubes of
OD range from 100 to 1,625mm, wall
thickness from 7 to 250mm, length
up to 6,250mm, in more than 200
grades of steel, alloys, cast iron, bi-
metallic combinations, as machined,
heat-treated, as well as articles of the
centrifugally cast tubes (furnace rollers,
bandages for crushers, metal moulds
for centrifugal casting, radiant tubes,
muffles, casings of hydraulic cylinders,
valves, motors, crane rope drums, rings,
slitters, press-moulds, flanges, pillars of
manipulators, wear-resistant tubes of
pulp-ducts, bushings for slush pumps,
construction columns, piles, etc).
Metal-removal
machine
tools,
facilities for heat treatment and
NDT allow the company to produce
centrifugally cast tubes and articles at
the level of worldwide standards. About
60% of products are exported. The
quality management system has been
certified in compliance with EN ISO
9001:2008.
The company’s plant can produce
fittings of the diameter range 24 to
1,420mm: elbows, bends, tees, pipe
crosses, reducers of carbon- and alloyed
steels. Some of these products are
supplied to thermal power stations and
atomic power stations. Thanks to the
possibility of independent manufacture
of moulding tools, new standard sizes of
fitting are constantly mastered.
R&PC Trubostal Ltd
– Ukraine
Fax: +380 5662 21190
Email:
trubostal@trubostal.com.uaWebsite:
www.trubostal.com.uaPlasma annealing and cleaning
for precision tubes
PLASMAIT GmbH, a supplier of plasma
heat and surface treatment lines for
wire, tube and strip production, has
introduced a new PlasmaANNEALER
for continuous annealing and cleaning
of precision tubes.
PlasmaANNEALER
has
been
designed for continuous heat treatment,
degreasing and oxide removal of
precision and thin wall tubes.
PlasmaANNEALER can be used on
a wide range of ferrous and non-ferrous
materials with OD range between 0.1mm
to 5mm. Thin-walled tubes with diameter
up to 10mm can also be annealed with
the new plasma process.
So far Plasmait demonstrated
successful annealing and surface
cleaning on tubes of various materials
including copper, copper alloy, stainless
steel and nickel alloy tubes.
PlasmaANNEALER is equipped with
vacuum system to ensure controlled
atmosphere and exceptionally low
usage of purging gas. The plasma-
heating zone is complemented with
appropriate length dwell zone to allow
for annealing of materials like stainless
steel and nickel, that require extended
time at temperature to achieve
complete annealing.
According to Plasmait’s R&D director,
Peter Ziger, the dedicated tube trial
facility is now available to all tube
manufacturers who strive to improve the
quality of their tubular products. Plasma
treatment will benefit
applications
with
demanding
surface
quality requirements or
challenging annealing
requirements.
Such
applications
are
usually found in sectors
such as medical,
precision mechanical,
electronics, aerospace
and energy sectors.
The tube manufacturers who adopted
plasma annealing have recognised the
value from low cost of ownership in
comparison to traditional tube or muffle
furnace.
The benefits of plasma treatment
include more than 50 per cent lower
energy use, ten times lower purging
gas consumption, the saving from dry,
chemical-free degreasing and surface
cleaning. Increased annealing speed by
the factor of five of more results in fewer
take ups and payoffs and lower cost of
maintenance.
Manufacturers of coated tubular
products may find plasma surface
preparation prior to coating or metallic
plating also an area of potential
interest.
Since the introduction of plasma
heat and surface treatment process
in the wire industry in 2003 Plasmait
continuously improved the process
and widened the application scope to
include annealing and surface treatment
of tubes and flat products.
With more than 52 deployments
of plasma treatment lines worldwide
Plasmait established itself as a trusted
supplier to the wire and tube industry.
Plasmait GmbH
– Germany
Fax: +44 7810 810 656
Email:
info@plasmait.comWebsite:
www.plasmait.comThe PlasmaANNEALER