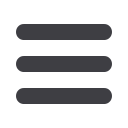

Feature
Steel wire, rod & rope production
November 2012
45
www.read-eurowire.comWorldwide appeal
Nevatia Steel & Alloys is an ISO 9001:2008, ISO 14001:2004 & OHSAS 18000:2007
accredited company, incorporated in 1988 for manufacture of stainless steel wires.
The company’s manufacturing facilities are strategically located close to the port of
Mumbai, India, and have a capacity of 9,000mt per annum.
Nevatia Steel wires are manufactured in
compliance with international standards of
quality and are in accordance with customers
stringent specifications. Wires are made in a
variety of grades (AISI 201, 202, 204Cu, 304,
304L, 316, 316L, 302, 303, 302HQ, 314, 321,
ER308L, ER309L, ER316L, ER 347, 310, 410, 420,
430, 430L, etc) in the size range of 0.10mm to
12mm in wire and in the size range of 2mm
to 6mm in bright bars, having demanding
applications in various fields like braiding,
knitting, weaving, cold heading, redraw, spring,
electro-polish, nails, staple wire, MIG, TIG, core
for welding electrodes and general purpose.
Over the years, its products have been exported
to a large part of the international community with major destinations including North
and South America, Australia, Canada, Europe, South Africa, Israel, Korea, Turkey and
Vietnam.
The Nevinox
®
brand MIG (GMAW) and TIG (GTAW) stainless steel filler welding wires
have recently been accredited with Deutsche Bahn (DB) approval in addition to
prestigious approvals from Bureau Veritas for marine applications, TUV for pressure
vessels and equipment and the CE Mark.
Nevatia Steel & Alloys Pvt Ltd – India
Website
:
www.nevatiasteel.comAlloy Wire International is a manufacturer in
exotic alloys like Inconel, Monel, Hastelloy and
Nimonic, which are used for the production of
springs, specialist seals, fasteners and other
demanding applications for industries where an
aggressive environment is encountered. Starting
from as large as 21mm wire, they make the wire
(either round, flat or shaped) to any customer
size down as far as 0.025mm. Spring makers and
other customers like the fact that there are no
minimums – with some customers ordering just
three metres of wire for the job in hand.
AWI has won worldwide customer accreditation
for making and delivering wire quickly – with
a typical turn around time of three weeks.
And when that’s not quick enough – for that occasion when, for
example, an aircraft or oil platform or naval vessel needs a spring
or springs within days, AWI manufactures the spring maker’s
wire via its emergency manufacturing service.
AWI is an expanding company. Its recent investments in brand
new equipment such as multi-zone annealing furnace and
250kN Zwick tensile tester, and 100 per cent factory expansion
are part of its programme to retain preferred supplier status for
the long-term future.
▲
The Alloy Wire International plant
AWI’s shaped wire division has seen similar commitment to
its future with the acquisition of a new larger factory, the
installation of CNC equipment, roll profile grinding and wire
straightening and cutting machines.
Its customers are as diverse as model rail profile to wire profile for
aero engines.
AlloyWire International – USA
Website
:
www.alloywire.com▲
Meeting international standards
Exotic alloys and
emergency service