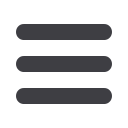

November 2012
58
www.read-eurowire.comPhoto: bigstockphoto.com – ‘The Chrysier Building’ by SongquanDeng
New line for CAP
CAP Technologies has started the first Electro-Plasma cleaning and
coating line for processing multiple strands of wire rod.
The EPT plant is located in Denham Springs, Louisiana, USA, and will
process commercial wire products, high tensile armour wire, spring wire
and PC strand wire. Annual production, which began on 1
st
September,
will be 25-35,000 tons.
The EPT process employs a first of a kind atmospheric plasma process
which allows for the in-line cleaning of mill scale, rust, complex oxides,
coating (single metals or alloys) and drawing of the coated material
without the loss of coating material and without the loss of any
mechanical properties.
Coating does not cause any loss of tensile strength, which occurs during
HDG. Zinc coatings have been proven to provide at least three times
the life of HDG coatings at approximately one half the coating weight.
Also proven, EPP processing, cleaning and coating does not under any
circumstances cause hydrogen embrittlement. The process is suited for
both ferrous and non-ferrous materials. Most importantly, the process is
a GREEN technology, closed loop system.
In addition to the production line, CAP has created a complete
multi-faceted research line capable of processing wire rod, wire and
stranded fine wire to 0.3mm diameter along with odd shaped parts and
pieces for applications outside the wire rod industry. Single wires can
be as small as .325mm in diameter.
CAP Technologies, in addition to the current 55,000ft
2
facility, recently
acquired additional land that will house CAP Engineering, due for
start-up in the latter part of 2012.
CAP Technologies – USA
Website
:
www.captechnologiesllc.comShaft-less series pay-offs
and take-ups
Huestis Industrial’s new shaft-less series pay-offs and take-ups are
efficient and “Huestis rugged”, featuring a small footprint allowing the
customer to install them in “tight” places, where manufacturing space is
at a premium.
They are capable of handling package sizes from a 12" spool up to a
36" reel, as well as weights up to 2,500 pounds. These are offered with
multiple options and possibilities, tailored to the customer needs.
Pneumatic, hydraulic, and electric versions are available allowing
customers to define the solution that will work best for their
manufacturing processes.
This series was developed to address the needs of circuit-sized
production. Huestis has allowed the customer to have single or multiple
units that can be dropped in place and they are able to meet a variety of
conditions.
The ability to handle a small spool all the way up to a full size
production reel gives the customer a machine that can do it all.
They can be as simple or sophisticated as the customer requires. The
company’s engineering department is available to design each pay-off
or take-up to suit and is backed by warranty and outstanding customer
service.
Huestis Industrial – USA
Website
:
www.huestis.com