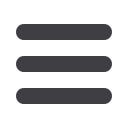

PRODUCT News
40
MODERN MINING
February 2016
The recently launched semi-mobile
Bradford Breaker was welcomed by
delegates at the Tenova TAKRAF Africa
Open Day held recently at the company’s
regional Client Support Services office in
Middelburg, South Africa.
The Open Day showcased a range
of advanced technologies supplied by
Tenova TAKRAF Africa, highlighting its abil-
ity to provide innovative solutions from
pit to port. These include the ‘monster
machines’for opencast mining, stockyards
New technology on display at Open Day
and ship loading/unloading, which are to
be found in major operations throughout
the globe, crushing and screening sys-
tems, the ingenious Tenova TAKRAF Africa
developed modular overland conveyor,
and the Dust Solutions Incorporated (DSI)
and Magaldi Superbelt® technology.
Bradford Breakers, sold under licence
from Terrasource Global in the USA, have
been extensively applied on South African
coal mines since being introduced to the
local market in the 1980s, proving highly
effective in simultaneously sizing and
cleaning raw coal. Developed origi-
nally for the American market and
its softer coal, Tenova TAKRAF Africa
has drawn on its wealth of experience
in the local industry to modify and
enhance the Bradford Breaker to make
it an appropriate choice for the difficult
coal of the South African market.
Particularly suitable for the junior
and small miners who are increas-
ingly exploiting the small coal
resources that remain, the most
recent development, the semi-mobile
Bradford Breaker, offers the benefits of
the breaker in a more compact machine
mounted on a skid. This allows for ease of
transport to move the Bradford Breaker
as mining progresses to another block
Mounted on skids, the
semi-mobile Bradford
Breaker was highlighted
at the Tenova TAKRAF
Africa Client Open Day
in Middelburg.
or resource, the ability to position the
Bradford Breaker as close as possible to
mining operations, therefore reducing
conveying costs, and reduced civil works
as the unit can be placed directly into posi-
tion on the skid.
Based on an ingenious design, the
Tenova TAKRAF Africa modular overland
conveyor is a breakthrough in conveying,
consisting of concrete modules precast at
the project site and fitted with idler frames
and brackets. These are easily and quickly
placed into position after the conveyor line
has been surveyed, with only a prepared
terrace required and no civil footings.
“The positive response we received
from our customers at the Open Day in
Middelburg underlines the importance
the industry places on Tenova TAKRAF
Africa’s innovative technology offering, as
well as our commitment to staying close
to our customers, “ says Riccardo Tonini,
Managing Director, Tenova TAKRAF Africa.
“Our network of offices, which covers our
headquarters in Spartan, Gauteng, and
regional offices in the Northern Cape
and Mpumalanga, ensures we provide a
comprehensive service from equipment
supply to aftermarket support, based on
an in-depth understanding of the spe-
cific requirements of the local mining
operations.”
Tenova TAKRAF Africa, tel (+27 11) 201-2300
Field tests on fuel filter exceed expectations
Advanced nano-fibre technology exclu-
sively developed by Cummins has –says
the company – been proven to dramatically
extend oil drain intervals, improve overall
efficiency and decrease the total cost of
ownership on OEM machinery and equip-
ment operating in the harsh South African
mining conditions.
The latest breakthrough from the com-
pany’s filtration division is the Fleetguard
FH239 Series Industrial Pro diesel fuel fil-
tration system and all-in-one fuel/water
separator, which was launched locally at
last year’s Mining Indaba, following suc-
cessful trial runs at mine sites over an
18-month period.
According to Cummins Fleetguard
Technical Sales Manager Gerald Annandale,
the product has been tested at numerous
mine sites across South Africa and has
exceeded all expectations. “In line with ISO
4406 cleanliness standards, fuel must be
inspected in laboratory conditions to deter-
mine its cleanliness before it is discharged.
The minimum level is 18/16/13, although
mining operations prefer 16/14/12,”he says.
“During extensive testing, the Fleetguard
FH239 Series Industrial Pro diesel fuel filtra-
tion system achieved its objective of 12/9/6,
before eventually going down to an incred-
ible 10/9/5. This is the cleanest fuel I have
ever seen, which will prove highly benefi-
cial to machine productivity.”
Cummins tested 200, 250 and 300-ton
trucks operating on different coal mines.
The objective was to achieve 1 000 hour
service intervals, as many mines were only
achieving between 250 and 750 hours.
Annandale reveals that the product com-
fortably got to 1 000 hours for all filtration,
and even achieved 2 600 hours on one
truck at first stage filtration.
According to Annandale, a traditional
engine has a 25 000-hour life expectancy
before a total rebuild is required. “This new
technology can extend this number to
over 33 000 hours,” he says. “This results in
greater productivity, less money spent on
labour, while downtime for servicing is also
reduced.”
The FH239 provides easy maintenance
with its self-priming port. By simply spin-
ning off the cap, users can pour in fuel
and restart the engine with clean, filtered
fuel. The clear cover tells users when not
to change their filter and offers a window
into the system to see fuel condition and
flow. This is Cummins’ patented ‘Seeing-is-
Believing’ technology, which is said to offer
superior effectiveness in removing water
and contaminants from the fuel system,
while ensuring that filters can be changed
within a matter of minutes.
Cummins, tel (+27 11) 589-8400