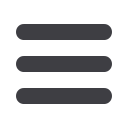

108
M
arch
2011
www.read-tpt.com›
I
nspection
, T
esting
& Q
uality
C
ontrol
Maschinenfabrik Liezen und Gießerei GmbH
Fabriksplatz 1, 4662 Steyrermühl, Austria
Phone: +43 7613 8883, Fax: +43 7613 8883 30
E-Mail:
saegen.fraesen@mfl.at,
www.mfl.at- Removal of the ID and OD welding seam
scarf of large-diameter pipes over
a length of 400 mm fully automatically
- No production of swarf
- Exact measuring of the welding seam by a
scanning device
Visit us!
Tube Russia, Moscow
May 23 - 26, 2011
Austrian Pavilion
www.mfl.atWelding seam processing machine
NOV Tuboscope, USA, is a supplier of tubular
inspection services and equipment for the
petroleum and pipe manufacturing industry.
The company’s range includes the Amalog
®
and Sonoscope
®
electromagnetic inspection
(EMI) systems, and the Truscope
®
, TruWall
®
and TruScan
®
ultrasonic (UT) inspection
systems.
The Truscope A/S system provides full-
body inspection across a large range of pipe
diameters. These pipes can be seamless
or ERW and manufactured from ferrous or
non-ferrous alloy materials. They can also
have a variety of end conditions: saw-cut or
cropped; plain-end; threaded; coupled; and
upset or non-upset.
With its combination of EMI (Amalog
and Sonoscope) and UT (Truscope)
techniques, the Truscope A/S satisfies the
stringent requirements of latest edition API
5CT, 5L and 5D. It also meets numerous
other international specifications for non-
destructive inspection of tubular products
for the energy industry.
The inspection system is composed of
two main sections – the inspection platform
and the computerised inspection electronics.
Mill inspection equipment
Placed within a pipe conveyor line, the pipes
are advanced to the inspection platform.
Mounted on this platform are pinch rolls
that contain the pipe and provide the driving
power to move it at a constant speed
though the three individual inspection
heads, or positioners. All three positioners
are mounted on track roller systems to allow
movement in or out the conveyor line for
pipe size changeover or maintenance.
Pipe to be inspected is first conveyed
through the Sonoscope inspection unit,
where a high-strength active magnetic field,
oriented longitudinally, is introduced into the
pipe. With the entering pipe end, a multi-
number of stationary detector assemblies,
or ‘shoes’, are brought into contact with the
outside diameter pipe surface. Flaws such
as transversely-oriented cracks, rolled-in
slugs and pits are detected.
The pipe is next conveyed through the
Amalog inspection unit, which is equipped
with a dual-shoe detection system integrated
into a rotating magnetiser assembly. As
the pipe enters this unit, a high-strength
active magnetic flux field, circumferentially
oriented, is introduced into the pipe. The
rotating detector shoes then scan the outside
surface area of the pipe circumferentially
in a helical path. This method detects
flaws such as longitudinally oriented seams,
cracks, and overlaps.
The pipe is then conveyed through the
Truscope inspection unit, which identifies
internal and external flaws and wall thickness
variations by utilising ultrasonic sound waves
coupled to the pipe surface by water. As with
the Amalog, the Truscope is equipped with
a multiple-shoe detection system. As the
pipe enters the rotating assembly, water is
applied to the outside pipe surface to provide
the acoustic coupling required for ultrasonic
inspection. The detector shoes are then
brought into contact with the outside pipe
surface to scan it in a helical path.
The Truscope can be configured to
detect longitudinal, transverse and oblique
defect orientations, and out of tolerance
wall thickness variations and laminations.
Pipe defect indications are transmitted from
the inspection platform to the computerised
inspection electronics for software analysis
and reporting.
NOV Tuboscope
– USA
Email:
millndt.systems@nov.comWebsite:
www.nov.com