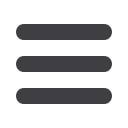

developments
products &
www.read-tpi.comOctober 2010 Tube Products International
39
Terex Cranes, a leading crane
manufacturer, has purchased the new
Rösler RDR 500 pipe blaster for its
plant in Zweibruecken, Germany. At this
location Terex produces lattice boom
cranes with a payload of more than 300
tons, which can move under full load
(‘pick & carry’).
Models manufactured at the site include
the CC 8800-1 Twin, which can lift 3,200
tons and still move under full load. An
essential section of this type of crane is
the lattice boom that is fabricated from
steel tubes of different diameters and
lengths. The RDR 500 tube/pipe blaster
allows Terex to de-scale and de-rust
tubes with a length of up to 18,000mm
and a diameter of up to 500mm, prior to
flame cutting.
A major factor in choosing the RDR
was that Rösler had already supplied
a number of nearly identical tube blast
systems to OEMs and steel trading
companies. Another important point
was that Rösler was able to adapt
the machine design to the Terex
requirements by conducting processing
trials in the Rösler test lab. The trials
showed that the required degree of
cleanliness, according to the Swedish
Standard of SA 2.5 (‘near white’) surface
conditions are achieved in the machine
with travel speeds from 2 to 6.5m/
min due to the two high performance
Hurricane
®
H42 blast wheels, which are
driven by 22kW motors. These easy-
to-maintain single disk blast wheels
are mounted sequentially on the blast
chamber.
The blast chamber itself is fabricated
from wear resistant manganese steel.
The precisely defined
blast angle ensures that
the required blast results
are consistently achieved
in the specified time, even
with tubes of a relatively
large diameter. Since the
Terex specifications only
call for the blast cleaning
of the outer tube surface,
the open tube ends are
masked. However, Rösler
also offers solutions for
applications where blast
cleaning of the inside and
outside of the tubes is
required.
Transport of the tubes
through the blast machine,
which is equipped with an
entrance and exit vestibule,
takes place with two
18m-long roller conveyors
with a rated load of 500kg
perrunningmetre.Theblast-
cleaned tubes are directly
transported from the exit
vestibule into the flame cutting system.
Since the supplier of the flame cutting
system, HGG Profiling Equipment BV
from the Netherlands, and Rösler have a
long-term and friendly cooperation, the
interface issues between the controls of
the two systems were easily resolved.
Besides blast performance and a robust
machine construction, the maintenance-
friendly design of the tube blaster was
another factor that convinced Terex to
buy the Rösler equipment. Very large
inspection/maintenance doors in the
entrance and exit vestibules, as well
as in the blast chamber, allow easy
and ergonomic access
to all areas requiring
maintenance.
The
maintenance door in
the blast chamber is
protected against wear
from the blast by slide-in
manganese plates that
cover the inspection
door without showing
any gap.
Rösler
Oberflächentechnik
GmbH
– Germany
info@rosler.com www.rosler.comEfficient blast cleaning of steel pipes
Universal
bronze
Ampco Bronze is a universal material
used in applications wheremarks, galling
or friction problems could decrease
quality in an unrepairable manner. The
alloys can provide solutions in bending
and forming processes, especially for
stainless steel and titanium, and where
severe load and wear conditions must
be resolved.
Ampco 25 is suitable for tube forming
(forming, welding and sizing rolls), while
Ampco M4 is ideal for tube bending
(mandrels, balls and wiper dies). Ampco
Metal SA claims that Ampco 25 has
significantly better compressive strength
(1,551 MPa) and average hardness (370
HB) than comparable materials.
Other advantages of the Ampco M4
material include no coating requirement,
no corrosion starting point and an
extended life time.
Ampco Metal SA
– Switzerland
info@ampcometal.com www.ampcometal.comSteel tubes are
transferred into
the shot blast
machine with a
roller conveyor
The two Hurricane H42 blast wheels are driven by 22kW motors