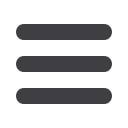

October 2010 Tube Products International
59
pipes
PVC, PE & XLPE
Owing to refinements made to the
thermoplastic polyethylene and the
pipes and fittings manufactured from
this material, the fields of application of
these products have increased. Pipes,
fittings and customised components can
be used in water supply and disposal
networks with pipe laying methods that
were inconceivable only 20 years ago.
In the past, the properties of PE for
industrial applications as well as water
supply and disposal systems were
developed with regard to internal
pressure resistance. This is reflected
by the basic standard DIN 8074/75 –
polyethylene (PE) pipes – PE 63, PE 80,
PE 100 and PE-HD.
In this context the material designation
and the load classification for pipes
refer to internal pressure creep rupture
strength (MRS = minimum required
strength) for 20°C, 50 years and the
test medium water. The underlying MRS
figures are 6.3 N/mm² for PE 63, 8 N/mm²
for PE 80 and 10 N/mm² for PE 100.
Owing to the soft pipe surfaces, PE pipes
were embedded in sand, in accordance
with the laying recommendations, in
order to prevent damage, and hence a
reduction in service life.
With the further development of pipe
laying methods, when installing new
pipes and rehabilitating buried water
supply and disposal pipelines it was
necessary to improve the material in
such a way that a high level of resistance
to external mechanical damage would
be achieved.
This goal was achieved thanks to
the development of bimodal PE 100
materialswith high resistance to slowand
rapid crack propagation. Classification
of these materials is set out in PAS
1075 – Pipes made from Polyethylene
for Alternative Installation Techniques:
Dimensions, Technical Requirements
and Testing.
In PAS 1075 (PAS = publicly available
specification), which is a supplement
to existing standards and guidelines,
there are three different types of RC
(resistance to crack) pipe.
Type 1: single-layer solid wall pipes
made of PE 100-RC
Type 2: pipes with dimensionally
integrated protective layers of PE 100-
RC
Type 3: pipes with dimensions
conforming to DIN 8074/ISO 4065 with
an outer protective casing; inner pipe
made of PE 100-RC
In order to meet the high demands
made by PAS, for the ‘Material’ approval
test the pipe must pass an FNCT (full
notch creep test at 80°C and a test
stress of 4 N/mm² in a 2% solution
of Arkopal N 100 for more than 8,760
hours) and a point load test (under the
same test conditions). The approval test
for the pipe must take the form of a
2NCT (2 notch creep test at 80°C and a
test stress of 4 N/mm² in a 2% solution
of Arkopal N 100 for more than 3,300
hours) and a point load test (under the
same test conditions but for more than
8,760 hours).
Based on this requirement profile it is
possible for the user and planner to
select a pipe that is technically and
commercially optimised for a particular
application.
On the basis of material specifications
and proofs it is possible to recommend
using pipes conforming to PAS
classification types 1 and 2 for sand bed-
free laying of PE pipes, eg in prepared,
compactable excavated trench soil. If
extreme loads are to be expected, as
with the alternative pipe laying methods
of pipe bursting and wash-boring, type 3
should be used. This largely corresponds
to the recommendations in DVGW
code of practice GW 321 (Controllable
horizontal wash-boring methods for
gas and water pipelines; requirements,
quality assurance and testing), and
GW 323 (Trenchless renewal of gas
and water supply pipelines by bursting;
requirements, quality assurance and
testing).
Simona AG is a manufacturer of
thermoplastic products, with production
facilities and sales offices around the
globe.
The company’s product portfolio
includes semi-finished products (sheets,
profiles, welding rods), pipes and fittings
as well as finished parts.
Author: Dipl-Ing Jürgen Allmann, product
manager pipes, Simona AG
Simona AG
– Germany
pipingsystems@simona.de www.simona.dePipes with increased resistance to
slow and rapid crack propagation