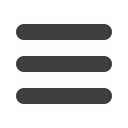

137
CHAPTER 6
TOTAL COST OF OWNERSHIP (TCO)
6.4 TOTAL COST ELEMENTS
Regardless of where a company applies total cost models, these models all
attempt to capture data beyond unit price. Like forecasting models, total cost
models almost always have some degree of unreliability. This section explains
how the categories of information that populate total cost models contribute to
this inaccuracy.
6.4.1 TOTAL COST DATA
The data that populate a total cost model can usually be segmented into three
categories. How the data are allocated across these categories affects the
reliability of the total cost model. The first category, and the one that presents
the highest degree of reliability, includes actual data. Unit price, insurance
on an overseas shipment, and tariffs are examples of actual cost data when
dealing with international suppliers. Few, if any, total cost models will include
only actual data. The ones that do include are probably excluding some cost
elements or data.
The second category includes approximations or averages. The main
characteristic here is the data are based on figures derived from internal sources.
The challenge with many cost elements is that the cost of identifying the true cost
of something could outweigh the value of the actual data. Would, for example,
a detailed study be conducted to identify the true cost every time a late delivery
occurred? The benefits of identifying the true cost of non-conformance may be
outweighed by the cost in time and resources required to undertake the study.
Overcoming this issue can result in the identification of various costs categories
or accounts with standard or average charges applied whenever there is a need
to allocate a charge.
The following illustrates the use of averages. In a recent year, 50 late supplier
deliveries cost a buying company an estimated R500 000 in total non-
conformance costs. The average standard charge in the total cost system for a
late delivery, therefore, becomes R10 000 (R500 000/50) per occurrence. Other
cost categories could apply standard or average charges per hour. Correcting a
minor defect in a supplier shipment might require 12 hours of labour. The model
can include standard labour rates per hour. The usual warnings about using
averages apply. A wide dispersion of true costs around this average creates a
concern that the average charges may under- or overstate the cost.
The least reliable total cost data are based on assumptions. Assumptions come
from external sources that form the basis for applying total costs. Let’s say a
study by researchers at a university concluded that it costs R150 every time a
buyer issues an order. Therefore, every time a buyer issues a material order
to a supplier, a R150 charge is applied to the total cost model for that item. But
does the R150 charge really apply to what happens at every organisation?
What if one company relies extensively on Electronic Data Interchange (EDI)
to reduce ordering costs while others in the study do not? It is important not