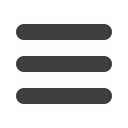

141
CHAPTER 6
TOTAL COST OF OWNERSHIP (TCO)
carrying costs are 24% annually, which the company must apply to the dried
fruit that is held in storage.
When a container of dried fruit is required at the Chefs Supply processing facility,
a local freight company will deliver the container at a cost of $275 per container.
Additionally, Chris estimates the cost of incoming receiving and quality control
procedures to be $4 per pallet. He further estimates that the company will incur
a 3% loss of the total purchased fruit. This loss will result from the nature of the
product, the supply chain distance involved (as in transit damages), and the
longer-term effects of storage.
Chris also determined, in conjunction with the industrial engineers in the
processing facility, that the historic yield of dried fruit when blended into various
products is 98%, which means that the company wastes an additional 2% of
the product by volume. This loss is not recoverable and is in addition to the
3% loss mentioned earlier. Some companies may exclude this yield loss from
the total landed cost calculation because it occurs during processing. Other
companies may also include the effect of payment terms or rebates provided
by the supplier. It is difficult to find two total cost models that include exactly the
same cost elements since no standard exists defining what these models should
contain. Finally, in addition to the costs noted above, corporate accountants at
Chefs Supply require that a 17% assessment on the unit price of the dried fruit
be included to cover general and administrative overhead costs at Chefs Supply.
With any total cost model the challenge involves getting complete and reliable
data. Chris must identify and collect the data he requires before he can develop
a cost model that progressively builds up the total cost per kilogram. Companies
that undertake this build up often find that their estimated total cost far exceeds
the more obvious unit price. Who can possibly know precisely the true cost of
international purchasing without undertaking this kind of exercise?
Table 6.2 provides some important information, such as annual usage (i.e.,
demand), that is required to calculate the per kg cost for each cost element.
Table 6.2:
Total dried fruit requirements [8].
Equals …
Dried fruit per bag (one bag
inserted into one box)
50 kg per box
40 boxes per pallet
2 000 kg per pallet
20 pallets per ocean shipping
container
40 000 kg per container
One container required per
month
480 000 kg of dried fruit required annually
(40 000 lbs x 12)
Table 6.3 presents the analysis that arrived at the total cost per kg of dried fruit.
The table also includes explanations for the determination of each cost.