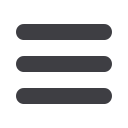

30
Mechanical Technology — August 2015
⎪
Local manufacturing and beneficiation
⎪
U
nison has won an order for a
custom-designed tube bend-
ing machine and special tool-
ing from Cybex International,
a manufacturer of physical exercise
equipment. Incorporating a unique servo-
driven wiper die mount, the machine
has been specifically designed to enable
Cybex to reduce waste material costs
by eliminating the need to cut shorter
tubular parts to length after bending.
Cybex produces a diverse array of
physical exercise machines at two large
state-of-the-art manufacturing facilities in
Medway, Massachusetts and Owatonna,
Minnesota. Its unique machines are de-
veloped with the help of exercise science
principles to be biomechanically correct
and generate optimum results with mini-
mum stress on the body.
Nearly all Cybex exercise equipment
is based on high quality tubular steel
framework, most of which is produced at
the Owatonna plant. The framework is a
highly visible part of the brand image and
therefore needs to combine an aesthetic
look and feel with structural strength. To
achieve this, Cybex constructs frames
from three different sizes of robust
11-gauge steel tubing, using a variety of
proprietary tube profiles including flat-
sided oval and compressed octagonal
shapes. Producing smooth, wrinkle-free
bends in these types of tubular profile
is technically challenging and demands
considerable expertise.
Cybex currently uses hydraulic tube
benders to handle the bulk of its produc-
tion needs, together with a single all-
electric CNC machine for more complex
parts that require multiple bends with
different radii. The tube parts range in
length from two to 10 ft and involve a
diversity of bends – from shallow curves
to tight bends with a centre-line radius as
small as 4.8 inches. Most parts require
bend accuracies of ±1.0˚ or better, to
help achieve end-to-end positional toler-
ances as tight as 0.03 inches.
After bending, the parts are welded,
Unison is supplying Cybex with a custom tube bending machine that will be based on a 4-inch multi-radius
Breeze model, with multi-stack tooling, laser spring-back correction and a unique swing-away wiper die.
Cybex will use the Unison tube-bending
machine to produce high quality tubular
steel framework for a diverse array of
physical exercise equipment.
Tube bender eliminates waste
for exercise machines
A Unison tube bender with a unique swing-away wiper die that facilitates
waste-free bending of short and complex tubular shapes has been chosen
by Cybex International, the manufacturer of physical exercise equipment.
cleaned, shot blasted and powder coated.
To ensure that the final product is un-
blemished, every stage of this process is
subject to stringent quality control.
Parts with complex bend shapes are
produced in small batch sizes – typically
of between 12 and 30 – on the compa-
ny’s existing CNC bending machine. Like
most rotary drawtube benders, this is
fitted with a stationary wiper die to help
control material flow and prevent tube
collapse during tight radius bending. The
permanent presence of the die imposes a
limit on the minimum length of tube that
can be bent. This means that to produce
short parts, Cybex has to use overly long
tubes and then cut them to length after
bending. This has several drawbacks:
it is time-consuming – it is much more
difficult to cut a formed part than a
straight tube – and demands additional
processing and quality control stages. It
also creates material scrap, which is ex-
pensive and at odds with the company’s
commitment to environmentally respon-
sible manufacturing practices.
The custom-bending machine that
Unison has designed will bend these
complex and short tube shapes without
generating cut-off waste. Instead of a
stationary wiper die, Unison’s machine
uses a unique swing-away tool mount,
which – like all motorised axes on the
machine – is driven by a software-
controlled servomotor. Moving the wiper
die away from the pressure die towards
the end of the bend cycle allows the tube
feed mechanism to be driven closer to
the rotary bending head, facilitating fully
automated production of short parts.
The new machine is based on a 4-inch
(100 mm) all-electric CNC tube bender
from Unison’s Breeze range. It has also