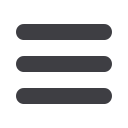

4
Mechanical Technology — August 2015
⎪
On the cover
⎪
“
P
owermite focuses on the
electrical and mechanical
aspects of moving machin-
ery,” begins Marks. “We
supply a wide range of products to help
machines move freely and safely: mobile
machinery, conveyors, cranes and bulk
materials handling machines
such as stacker reclaimers and
ship loaders all require power,
cabling and sensing solutions
to allow them to function ef-
fectively,” he says.
The company was founded
in 1967 with a competent team
of people to service the grow-
ing need for flexible cables and
power solutions for mobile ma-
chinery. “By 1981 Powermite
had grown into a ‘one stop’
supplier for electrical crane
materials and, today, has close
to 300 people working across
three divisions: Cables and Accessories;
Materials Handling; and Plugs and
Sockets,” Marks reveals.
Stemming from a partnership with
the French multinational, Delachaux
and its Conductix operation, which is
dedicated to the transmission of energy
and data for industrial equipment and a
global supplier to the materials handling
industries – drag chains, cable reelers slip
ring housings, etc – Powermite became
involved in supplying equipment such
as ship to shore loaders and electrified
rubber tie gantries (ERTGs). “We electrify
the systems that pick up and move cargo
with reelers or conductor bars, for ex-
ample, to overcome the need to use more
costly diesel-power,” he tells
MechTech
.
Lasstec load sensing
The Lasstec load sensing system is a one
of the newer Conductix innovations and is
designed to streamline the acquisition of
weight data from shipping containers so
as to improve port handling efficiencies.
“Poor control of the weight of individual
shipping containers as well as the weight
distribution of containers on a loaded
ship can lead to overloading and ship
Powermite’s Materials Handling Division, a proud distributor of Conductix products
for more than 40 years, recently launched Conductix’s Lasstec container weighing
solution. This fibre-optic based system is mooted to make it easier for
ship terminals to comply with the new International Maritime
Organisation’s (IMO) legislation that will make container weight verification mandatory
by July 2016.
MechTech
talks to Powermite director Donovan Marks (left) about the
technology and its advantages.
New IMO container weight verification requirements
mean that, after July 2016, every container will have
to be accurately weighed before it can be loaded onto
a ship.
Fibre-optic spreader beam
for safe and efficient container handling
instability at sea,” says Marks.
New IMO law comes into force in
July 2016, which includes new con-
tainer weight verification requirements
for entry into a ship’s loading manifest
prior to loading. This will mean that ev-
ery container will have to be accurately
weighed before it can be loaded onto a
ship,” Marks reveals.
To overcome this problem, the IMO
has decided to make container weight
verification mandatory. The Safety of
Life at Sea amendment for mandatory
container weight verification prior to load-
ing containers onto a vessel was initially
accepted by the IMO back in 2013, and
this amendment will enter into force in
July 2016.
“The amendment makes it the ship-
per’s responsibility to declare the correct
container weight. If the shipper does not
declare the correct container weight, then
the terminal shall weigh the container
and charge the shipper,” Marks informs
MechTech
.
The issue arises as to where to weigh
the containers for verification purposes.
Weighing containers at weigh bridges
at the entry point to a harbour can be
cumbersome, since it creates queues
of trucks at the terminal entrance, each
typically carrying two 20-ft containers.
“To stop and weigh every container on
entry could further delay ship loading,
increasing harbour costs and reducing
efficiency,” he suggests, adding that