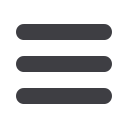

Technology News
www.read-tpt.comJ
uly
2013
53
ArcQuality convinces Outotec
MINERALS and metals processing
technology company Outotec, Finland,
has installed an ArcQuality welding
quality management system from
Finnishwelding equipment manufacturer
Kemppi Oy, for welding operations in its
Turula engineering workshop. Outotec
is also planning to expand the use of
ArcQuality to its other workshops.
Plant
director
Ilkka
Hiltunen
commented that quality control for
welding is a key part of the workshop’s
activities: “It is easier to improve the
quality when production is in one’s own
hands. ArcQuality is a modern, up-to-
date way of ensuring quality control.”
Outotec’s production development
manager, Kari Koistinen, believes that
high welding quality is achieved by
making sure that the company employs
excellent quality-control processes. Mr
Koistinen said, “The manufacturer has
to provide the client with the quality
required and one needs to be able to
prove the quality of the product to both
the client and the quality assessment
organisation.”
Outotec Turula has a 21,000m
2
production facility along with an area
for pre-treatment. The Turula workshop
has around 70 MIG/MAG, TIG and MMA
power sources. The ArcQuality system
provides a method of verifying welding
quality. Mr Hiltunen praised the system,
explaining, “Previously, there were
cases in which the client required data
on who welded what and when. Now,
the system collects all the required
information automatically.” Mr Koistinen
added, “ArcQuality is a highly suitable
tool for the management staff, since it
enables immediate intervention when
there are noticeable deviations from the
norm.”
Welding co-ordinator Rauno Kakkola
believes that ArcQuality should become
a mainstay of welding schools and
that it also affects how management
operates, because real-time reports
are readily available. “Management
must make sure that welding procedure
specifications are available. At first, the
system requires guidance and training.
It is used to make everyone’s work
transparent and employees should not
feel that there is extra pressure on them
because of this,” Mr Koistinen stated.
Implementing the system requires
an active approach from the company
deploying it. Mr Kakkola emphasised
that the principles of the system must
be taught to each
welder individually
and the smart reader
device must become
a personal work tool
for every welder. Mr
Hiltunen added, “We
must explain to the
welders why we are
using the system in
the first place.”
ArcQuality
is
provided as a cloud
service via a secure
server, so the system
is accessible from
anywhere and does
not place a burden
on the company’s
own network. Updates and new features
can also be quickly implemented.
With the ArcQuality service, it is easy
to make sure that the entire welding
process is carried out in accordance
with welding procedure specifications.
Monitoring by this service also ensures
that the welders are qualified to perform
the tasks they are assigned. Possible
deviations are reported automatically
and in real time.
The system can also be used in
preparation for maintenance operations,
and the smart reader compiles quality
data even for weld-specific traceability,
if necessary.
Kemppi Oy
– Finland
Fax: +358 3 899 428
Email:
export@kemppi.comWebsite:
www.kemppi.comNew rotary draw bender
IN confirmation of its on-going
commitment to meet the market’s
growing needs, Ercolina has launched a
new and improved rotary draw bender:
the TB130 Top Bender.
The TB 130, with its 130mm (5")
capacity is suitable for producing
consistent quality bends in large pipe,
tube, squares, solids and other profiles.
A strong cast iron design matched
with high precision planetary reducer
ensures quality, repeatable bends.
An interactive PLC touch screen
control offers easy access to auto and
manual operating modes, programming,
system diagnostics and multiple
language capability. Programmable
bend angles range from 0° to 180°, with
up to 12 bends per program.
Other features include independent
springback compensation for each
bend; USB port for software updates
and unlimited program storage; digital
display of counter bend die axis and
bend angle; bends to CLR as small
as 2D; patented quick-change tooling
system with multiple radii available; and
no hydraulic components, reducing cost
and improving bend accuracy.
Auto load sensing improves bend
productivity while protecting machine
components.
Electrical components are UL, CSA
and CE approved.
CML International SpA
– Italy
Fax: +39 0776 404801
Email:
info@ercolina.itWebsite:
www.ercolina.comThe bar code from the welding procedure specifications is read into
the system before welding