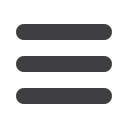

Roofing, Ceilings, Insulation & Cladding
T
he 17 500m² hub includes a self-
contained training centre, four
small factories, educational fa-
cilities, kitchens, bathrooms etc. The
main contractor GD Irons awarded
the contract for roofing to Max-Span
Roofing who specified MiTek Ultra-
Span system.
Structural engineer, CassieGrobler
in consulation with MiTek, provided
the initial design and cost estimates
as well as providing various roofing
design options. Uwe Schluter, Busi-
ness Development Manager of MiTek
says that most of this project was
indeed done with Ultra-Span LGS
trusses even though some large BC
loadings (steel with cross sectional
areas) were applied to cater for future
applications, representing 17 500m
2
of area (or approx. 78% of the total)
with the balance being done in mild
steel structures.
The Light Gauge Steel (LGS) Ultra-
Span structures achieved a very
respectable low mass of only 6.3kg/
m2 of roof area. It is this low weight
of the Ultra-Span roof structure that
enabled substantial savings to be
realised on thewhole project through
support structure savings, as well as
installation time savings although no
cranes were required during any of
the LGS roof erection phases.
Schluter explained that the roof
structure was rolled out in phases.
It could have been completed even
quicker had the building work been
able to keep up with this pace. “The
Ultra-Span roof structure greatly as-
sisted with the overall timing of the
project being kept on track. Initially
a crew of 14 workers assembled the
trusses and roof erection work, but
during the last two months of the
project as building work completion
increased, an additional six-man
team was added to the roof erection
team.
A further advantage that the Ultra-
Span system provided Max-Span
Roofing (LGS assembly and installa-
tion contractor), is that it was pos-
sible to utilise the existing ordered
materials with some very small
modifications. On some blocks, the
building dimensions differed fromthe
original plans as well as the addition
of extra point loads on the BC of some
of the trusses – even though none
of these were originally designed or
manufactured for this.
This feature of Ultra-Span is possible
due to the fact that the materials are
not pre-punched (for joint connec-
tions) and therefore allow the free-
dom for some length adjustment as
well as the simple insertion of splices
should this be required. Likewise, the
extra point loads on the BC of some of
the trusseswas easily accommodated
by the addition of some extra screws
or where a different web size was
required. All of the above steps were
obviously taken after full re-analysis
of the effected trusses.
Schluter says that although this
particular roof structure is not re-
ally complicated or unusual, it is still
one of the largest single project roof
structures done in LGS, with all par-
ties involved being totally happy with
the overall result.
Schluter says: “With amanufactur-
ing facility in Gauteng and regional
offices in Cape Town, Port Elizabeth
and Durban, MiTek is best placed to
supply the building industry with the
widest range of timber connectors
for both roof truss manufacturers
and retail stores. Our expertise lies in
three areas, our integrated software
packages, our fully designed builders’
products that are manufactured in
accordance with Dekra ISO9001:2008
certification specifications and our
people, many of whom have been
with MiTek for more than 25 years.”
■
Riversands Incubation Hub
The Riversands Incubation Hub is one of the largest roofing projects
undertaken using Light Gauge Steel construction.
July 2015