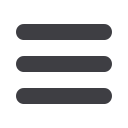

April 2017
MODERN MINING
35
feature
MODULAR PLANTS
African mining
Above:
A module designed
by Fluor in transit from the
fabrication yard to the Letl-
hakane site in Botswana.
Left:
A module designed by
Fluor loaded and ready for
transportation to site.
also result in significant capital cost savings for
our clients, and reduced site work contributes
to a much safer working environment.”
Typical modules for the mining industry
include process facilities, crusher and conveyor
modules, and pipe racks. “Modular plants are
fast moving from smaller pre-fabricated units
to macro units, where up to 90 % of a facility
can be pre-assembled and commissioned prior
to transport to site,” says Escalona.
He points out that the company’s level
of achievable offsite work has significantly
increased since using Fluor’s patented and
innovative 3rd Gen Modular Execution
SM
strat-
egy. “When so much of a facility is modularised,
these site-assembled modules are essentially
‘plug and play’, allowing for final checks at the
module assembly yard.”
Fluor pioneered large-scale modularisation
in mining in Western Australia for the iron ore
industry, transporting a large number of mod-
ules by truck over a distance of 500 km inland.
The Fluor-led joint venture’s scope included
overall programme management activities and
EPFC services for specific elements of the mine,
port and rail works. Fluor designed and fabri-
cated 38 process plant modules. Among the
key benefits of assembling modules in purpose
built fabrication yards were limited construc-
tion activity and equipment on site.
In sub-Saharan Africa, Fluor has applied its
modular approach to design 60 process plant
modules and 106 conveyor and services gan-
try modules for Debswana’s Letlhakane Mine
Tailings Resource Treatment Project (LMTRTP)
in Botswana. Says Escalona: “The design of the
modules was tailored specifically around the
project size, location and client requirement.
They were assembled locally at a yard off site
and transported to the mine by road.”
Fluor was awarded the engineering phase
of the LMTRTP in 2014. The new 2 Mt/a
plant will recover the existing coarse diamond
tailings mineral resource and extend the life-of-
mine of the Letlhakane operation by 25 years.
The design of this stand-alone plant is cen-
tred on a modular approach. The main process
areas such as the Dense-Media Separation
(DMS), scrubbing and crushing buildings have
been designed in such a manner as to allow
them to be fully constructed from fit-for-pur-
pose modules, thereby accelerating project
execution.
“Fluor’s experienced project teams are ready
to assist clients in the oil and gas, mining and
metals, power and infrastructure industries
to assess their particular project design and
circumstances, and evaluate the merits of a
modular construction strategy,” concludes
Escalona.
Typical modules
for the mining
industry include
process facilities,
crusher and
conveyor
modules, and
pipe racks.