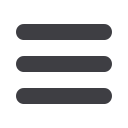

April 2017
MODERN MINING
39
MODULAR PLANTS
feature
fines recovery
Above:
An RC™
3000
in the
FLSmidth Qingdao factory.
Below:
The modular plant
consists of modules of
standard container sizes for
each of the various stages of
the process.
UG2 reef, as well as iron ore, mineral sands,
spodumene and coal.”
Terence Osborn, Commercial Manager for
FLSmidth Sub-Sahara Africa, says that access
to capital to fund projects is a major hurdle
in the minerals processing industry currently.
FLSmidth has realised the modular solution is
as much a technical issue as it is a commercial
one. FLSmidth in Sub-Saharan Africa is open
to investigate with its customers alternative
packaged tailored solutions, including an out-
comes-based model or a cost-per-tonne model
based on the additional recovery achieved with
the RC™ technology.
“Once the commercial offering is confirmed
with the customer, all that would be required
is for the end-user to pour a concrete slab and
provide 400 kW of power, feed water, a slurry
feed and takeoff. This could also be costed into
the financial model if required.”
Hazell says the RC™ technology and
modular plant offering is a game-changer for
the mining industry. “The modular plant has
the potential of putting 5 000 tonnes more per
month of product onto the floor than current
spirals technology, so the payback for the client
is significant,” he says.