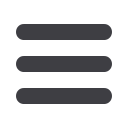

December 2015
MODERN MINING
23
GEOTECHNICAL
risk at Orapa
Inspecting the integrity of the drapery mesh system.
Two Decoilers specially designed for the project were deployed on the contract.
vehicular traffic into and out of the open pit.
One of the slopes that required rockfall miti-
gation extends over an area of 57 040 m
2
. The
linear horizontal length of the area is 320 m,
with the average height of the highwall slope
being 178 m. The second slope extends over
an area of 34 960 m
2
, with a linear horizontal
length of 330 m, with the average height in this
case being 106 m.
Wepex had previous experience of provid-
ing viable solutions to rockfall problems at
mines, having completed similar projects at
Debswana’s Jwaneng mine (a first project in
2010 of 54 000 m
2
and a second in 2013/2014
of 135 000 m
2
), as well as Anglo American
Platinum’s Mogalakwena mine in Limpopo
(where the area involved was 40 000 m
2
). With
all three of these projects, Maccaferri’s prod-
ucts and Melis & Du Plessis’ innovative design
were used, achieving the desired results, with
visible, quantifiable success.
Rockfall mitigation is not a recent require-
ment for open-pit mining activities. Various
factors such as natural degradation of the rock
mined, insufficient catchment areas, poor min-
ing practices and rainfall cause rockfall hazards
to develop. There are a number of mitigation
options available and all have variable time,
cost and quality implications.
One of the primary reasons a drapery sys-
tem was chosen for Orapa was the height of the
highwall slopes that required mitigation which
extended to over 180 m above the haul road.
The drapery mesh solution that Wepex
adopted prevents a significant number of rocks
from falling in the first instance or, alterna-
tively, in the case of rocks which have become
loose, intercepts them, allowing a significant
number to work their way to the bottom of the
drape wire mesh without impacting the normal
operation of the haul road. Many alternative
solutions adopt the approach of trying to ‘catch’
the rocks on their way down to the pit floor or
haul road. By the time these rocks have reached
the catchment devices (or missed them and hit
the pit floor or haul road) they have reached a
significant velocity!
Benefits of the drapery mesh system include
minimal to no environmental impact and the
fact that the quality and construction of the
Maccaferri drape wire mesh product used offers
a longevity that exceeds the projected require-
ments for mitigation of the areas.
The wire mesh chosen for the project needed