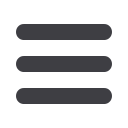

EuroWire – November 2009
39
technology news
“
ACID-FREE
PROCESS FOR STEEL
ROD CLEANING & SURFACE
PREPARATION”
“New Way to Draw Steel Wire
in the 21
st
Century”
DCCD process features:
• Eliminates acid, borax and precoatings
• Zero energy consumption
• Direct drawing from bare rod with no
speed limitation, for H/C and L/C
• New Lubricant Viscosity Control
provides exceptionally adherent coating
• Adjustable lubricant residual
• Zero lubricant waste
• Recommended for severe drawing
applications (spring, rope, bead,
CO
2
welding, PC strand, plating quality)
• H/C wire drawn at 18 m/s (3600 ft/min)
• Up to 8 times longer die life
• Exiting wire temp. 45°C (113°F)
• Greatly improved wire ductility
DECALUB
31, avenue de Condé
77500 CHELLES, FRANCE
Fax: +33 1 60 20 20 21
E-mail:
info@decalub.comWebsite:
www.decalub.comCANDOR Sweden AB
Tel: +46 11 21 75 00 Email:
info@candorsweden.comFax: +46 11 12 63 12 Website:
www.candorsweden.comclean wire
after drawing
candor
can do wire
equipment
Electrolytic plating
◆
Candojet hot water cleaning
◆
Electrolytic & Ultrasonic
◆
degreasing
Welding wire cleaning and
◆
copper coating
Pickling & phosphating
◆
The MM 85 rod breakdown machine was
developed by Niehoff to simultaneously
draw two copper, aluminium or alloy
wires to finished diameters of 1mm–5mm
at production speeds up to 38m/second.
It includes a quick-change drawing die
system, a fully-immersed drawing basin
with reliable separation of drawing
emulsion and gear oil via a mechanical
seal, and a touch screen-based user
interface and fault display.
MM 85 can be combined with the
two-wire version of an R 501 or an RA 501
continuous resistance annealer. The R 501
annealer was designed for copper wire,
while the RA 501 annealer is adapted
to the requirements of aluminium and
aluminium alloy wires. Both annealers are
designed for energy efficient operation.
Wires exiting the annealer are completely
dry. The entire wire path inside the
RA 501 aluminium annealer is covered
with protective gas to prevent oxidation
of the wire surface. A digital annealing
voltage controller ensures repeatable
and consistent wire annealing quality.
Freely programmable control systems
(PLCs) and standardised interfaces make
the drawing and annealing line easy to
combine with many spooling and coiling
systems. Niehoff has developed take-up
and spooling systems for the whole
range of wire drawing applications.
As a result of the design and control
characteristics, the wires drawn on
an MM 85 drawing line have similar
properties with very fine tolerances
along their entire length, and operating
conditions are characterised by con-
siderably reduced down times. Based
on 7,000 hours per year of operation
and 80% utilisation, wire production
outputs of up to 31,000 t/a for copper
wire, and 18,000 t/a for aluminium wire,
are possible.
Maschinenfabrik Niehoff GmbH & Co
KG – Germany
Fax
: +49 9122 977 155
:
info@niehoff.deWebsite
:
www.niehoff.deDrawing and annealing technology
Nextrom has developed a high-speed,
optical
fibre
colouring
line
to
improve productivity and flexibility
for manufacturers. The development
concentrated upon the design of key
line components to achieve colouring
speeds up to 3,000m per minute.
A robust mechanical and electrical
design, combined with optimised
tooling, an improved UV lamp system,
UV monitoring instrumentation and
increased spool sizes, provides the
capability to produce longer fibre
lengths with faster set-up. The result is
described as a significant productivity
improvement.
Previous developments of UV up-
coating and ring marking were
incorporated into the new design to
provide the flexibility to manufacture a
variety of products. The colouring line
consists of a large capacity spool payoff,
a dancer for payoff speed control and
a coating station, followed by a series
of high powered UV lamps below
the coater. The precision capstan is
located below the UV lamps. The fibre
passes through the dancer and tension
balancer, which reduces loops that
can cause OTDR steps, before being
precisely wound onto a large capacity
traversing take-up spool.
Optional ring marking and a range of
payoff and take-up sizes are available.
Nextrom Oy – Finland
Fax
: +358 9 5025 3003
:
info@nextrom.comWebsite
:
www.nextrom.comAdvanced colouring system OFC 52i
R 501 continuous resistance annealer from Niehoff
▲
▲