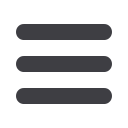

EuroWire – January 2012
48
News
Technology
Manufacturers today face a number
of production challenges based around
productivity, quality and cost reduction.
At the centre of this challenge, is the
ability for manufacturers to accurately
measure the length and speed of wire and
cable in order to better control sequential
printing or marking operations.
Traditionally, manufacturing plants have
used mechanical type encoders, such as
contact rotary encoders or tachometers,
to measure the length and speed of wire
and cable during production in order
to control the sequential printing on
products.
The outer coatings of cables are typically
marked with details including product
length in the form of metre or footage
marks, manufacturer’s name, product and
operating information.
Wires may indicate special numbering
or coding for identification purposes.
Customers rely on the accurate spacing
of this information to ensure the
manufacturer delivers the exact amount
of product as specified.
Customers also rely on the accuracy of
this information to perform critical tasks,
such as laying the correct amount or
length of wire or cable without needing
to re-measure it.
But contact encoders are prone to
mechanical and calibration problems
which result in costly measurement errors.
As such, wire and cable manufacturers
are looking to non-contact measurement
methods such as the LaserSpeed encoder
from Beta LaserMike to accurately
measure the length and speed of product
during sequential printing applications.
Manufacturers are realising productivity
gains with this technology by significantly
reducing
measurement
errors
and
improving process control. This article
gives an inside look.
Contact encoders face
real measurement chall-
enges during production
Depending
on
the
application,
mechanical
contact-type encoders face
a number of challenges in
wire and cable production
processes. First, mechanical
encoders must contact the
wire or cable in order to
measure the length and
speed of product during
production.
These
measurements
are
indirect
measurements, relying on the physical
contact between the mechanical encoder
wheel and the product’s surface. Length
is calculated from the amount of rotation
of the contact wheel. However, contact
encoders by their very nature have several
fundamental flaws that make them prone
to measurement errors.
Contact encoders are subject to slippage
and calibration changes caused by
variations in the diameter of the contact
wheel due to dirt build-up or wear. Since
the contact encoder is a mechanical
device, it also experiences mechanical
component failure from time to time –
requiring repair and re-calibration.
The measurement error of mechanical
systems will also change with production
conditions, requiring the line operator
to continuously check the spacing
of the print and then recalibrate the
contact encoder to keep the marks
within specification. Product length and
speed inaccuracies may be as much as
2%, or even greater, depending on the
application.
Products such as CAT, CV, power,
telephone, and other types of cables
are
very
expensive
to
produce,
and
manufacturers produce
millions of feet or metres
of wire and cable product
monthly.
A
two
per
cent
measurement inaccuracy
on this large amount
of product means the
plant can generate a
substantial
quantity
of
material
scrap
or
waste.
This
can
cost
manufacturers
a significant amount of money in
unnecessary expense. As such, length
accuracy is of paramount importance.
Non-contact approach eliminates
measurement errors
Non-contact
length
and
speed
measurement
systems
avoid
the
measurement pitfalls encountered by
mechanical contact systems.
The non-contact laser
encoder that allows
makers to accuratelymark
wire and cable products
▲
▲
LaserSpeed non-contact length and speed encoder
▲
▲
Contact method is prone to
measurement errors
By Jay
Luis,
the
worldwide
marketing
manager
for
Beta
LaserMike,
a
leading
global
provider of precision measurement
and control solutions for a wide
range of industrial applications
Continued on pages 50 and 51