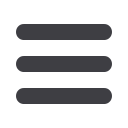

PRODUCT News
March 2016
MODERN MINING
47
Conventional chute design is often asso-
ciated with the uncontrolled discharge of
bulk materials, which is linked to increased
material degradation. Custom engineered
for individual application requirements,
Weba Chute Systems are successfully
moving materials in all commodity sectors
globally.
Mark Baller, MD ofWeba Chute Systems,
explains that a systems approach to bulk
solids handling design is essential to
ensure operational characteristics are
matched throughout the plant. By custom
designing each transfer point, individual
Weba Chute Systems can be configured to
suit each particular application.
“Our system uses a ‘supertube’, with a
cascade scenario, where 95 % of the mate-
rial runs on material at the same time in
a tumbling motion, rather than gliding
down the chute. We have found that glid-
ing particles cause extensive wear, while
the tumbling or rolling motion causes far
less wear. We have taken this a step fur-
Weba Chute Systems eliminate material degradation
ther by designing the internal angle of the
transfer chute to match the product with
the belt speed and in so doing product
degradation is greatly reduced or com-
pletely eliminated,” he adds.
The Weba Chute System uses a stream-
lined scientific approach to the dynamics of
bulk materials handling taking all aspects
such as belt speed, belt width, material
size, shape and throughput into account.
The custom design allows control of the
direction, flow and velocity of a calculated
volume and type of material in each indi-
vidual application and, at the same time,
drastically reduces dust.
“In essence, it is the absolute control
of material while being transferred that
will eliminate degradation. This requires
an in-depth understanding of how mate-
rial needs to be transferred and factors in
changes of direction, the impact during
these changes of direction and height of
transfer,” says Baller.
The geometry of the system should
be such that material is moved through
the chute system with gradual directional
changes and controlled velocity in order
to minimise impacts that lead to material
degradation and dust generation. In addi-
tion, discharge onto the conveyor system
must be correctly controlled and be as
close to the belt speed as possible.
Weba Chute Systems, tel (+27 11) 827-9372
Controlling the transfer of material onto the conveyor belt
guarantees increased cost savings for clients in addition
to an improved health and safety performance.