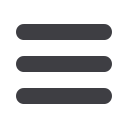

54
Wire & Cable ASIA – JulyAugust 2015
www.read-wca.comTemperature (°C)
Cable sample
Thermo couple
DC power supply leads
❍
❍
Figure 2
:
Cross-sectional temperature plot
❍
❍
Figure 3
:
Measurement setup
The model was set up to replicate the proposed
measurement method
[3]
, which allowed for a comparison
between theory and practice.
In order to achieve this, a five-cable linear configuration
was set up with the intention of providing a good
prediction of the thermal behaviour at the centre cable
without the need for including additional cables in a model
requiring higher computational resource.
Heat capacity at constant pressure, density and thermal
conductivity material properties were applied to represent
the constituent parts of the Cat6A 26 AWG U/FTP cable.
These properties were applied to the copper (Cu)
conductor, aluminium/PET (Al/PET) tape, Low Smoke
Zero Halogen (LSZH) jacket, and polyolefin insulation,
see
Figure 1
. Conduction, convection and radiation
heat transfer mechanisms
[5]
were accounted for in the
model.
Simulated electric energy was applied to one pair of
each cable in the model. A stationary solver was used
to determine the thermal behaviour for (a), a point at the
centre of one of the energised conductors (see probe
position in
Figure 1
), and (b), a 2D temperature plot of the
cross-section,
Figure 2
.
From the 2D plot, and as expected, the maximum
temperature of the arrangement is evident in the proximity
of the energised conductors.
Test method and results
The test method proposed by IEC Subcommittee 46C
[3]
was followed in order to establish the rise in conductor
temperature due to DC powering. This method involved
measuring voltage supplied and jacket temperature using
a 100-metre sample of cable wound onto a reel and
positioned within an environmental chamber fixed at 20°C,
see
Figure 3
. This method was followed using a sample of
Cat6A U/FTP cable with solid copper 26 AWG conductors,
as simulated in section 2.
The cable sample was conditioned at 20°C for at least
16 hours before testing. A thermocouple of J type was
positioned along the jacket at the halfway point of the
cable. Using a Keithley 2200-60-2 (60V, 2.5A) bench power
supply operating in constant current mode, a current (I)
of 0.6A was applied to the pair under test with the far end
of the sample short circuited. Temperature and voltage
data was logged at 15 second intervals using National
Instruments LabVIEW software
[6]
.
The temperature of the cable sample increased due to
the Joule heating effect, and after a certain time, the
temperature stabilised. At this point in time, the heating
due to the DC power input became equal to the radiated
power of the sample and the temperature was prevented
from rising further.
Conductor resistance was calculated based on voltage
immediately after the power was switched on (U
0
),
equation (1), and after the temperature had stabilised (U
T
),
equation (2). Change in (or delta) conductor temperature
(Δt) was then calculated using initial (R
20
) and stabilised (R
t
)
resistance, equation (3).
This methodology was repeated using four different
current (I) values, ie 1.0A, 1.4A, 1.8A and 2.2A.
Figure 4
shows the change in conductor temperature versus DC
current level simulated at the probe (see
Figure 1
) and
calculated from the measurement.
Results show a linear relationship with both delta
conductor temperature and current plotted on logarithmic
scales. Based on this relationship, it was possible to
apply an approximation, in the format Δ
t
=
x
*
I
y
, which could
be used to predict conductor temperature rise for current
values outwith the range measured. For the Cat6A 26 AWG
U/FTP cable, this approximation was found to be:
(INSERT IMAGE/CALCULATION 1 HERE)