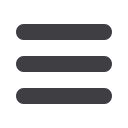

18
Mechanical Technology — November-December 2016
⎪
Materials handling and minerals processing
⎪
T
he contract to supply a pallet
shuttle system for the global
container transport and logistics
giant, Intermodal Cargo Solu-
tions, was awarded to APC against a
number of competitors due to its numer-
ous benefits and a design to aid the client
develop a final solution. This included a
sprinkler system, for which one of APC
Storage Solutions SA’s business partners
was used.
Intermodal Cargo Solutions had been
in talks with one of APC Storage Solutions
SA’s competitors and required an ad-
ditional service provider to propose and
quote on a similar solution. APC Storage
Solutions SA was approached and took
the time to understand all of the client’s
needs, including facility layout, load
units, pick rates and throughputs. The
fact that Intermodal was dealing with
various companies, each able to pro-
vide only a part of the overall required
solution, counted substantially in APC
Storage Solutions SA’s favour, as it was
in a position to manage the entire project.
With this information at hand, the team
submitted a design to meet the client’s
requirements, which led to the contract
being awarded.
About 110 containers are received
Africa’s leading warehouse storage solutions company, APC Storage
Solutions SA, recently completed the installation of a turnkey system for
Customs Franchised Container Freight Station Company, Intermodal Cargo
Solutions. Ettienne Meyburgh, GM for the company’s KZN region
and automation, highlights the systems advantages.
Above:
The ware-
house handles
approximately 5 500
pallets, with total
warehouse turnaround
achieved fortnightly.
Left:
The pallet shuttle conveys
pallets up to 1 500 kg at 1.3 m/s to desig-
nated storage bays within the racking lanes.
With rapid travel speeds of 1.3 m/s achieved with precise location accuracy, pallet shuttles maximise stor-
age and retrieval efficiency and prevent damage to the racking structure.
Turnkey storage solution
for Intermodal Cargo
by Intermodal fort-
nightly and 5 500
pallets are dis-
patched, resulting
in total warehouse
turnaround every
two weeks. “Our
proposed solution
meant that we needed
to take the standard operating
procedures, business rules and active
target rate of receiving and dispatch
into consideration, as well as receiving
and dispatch door locations. This was
necessary to allow the customer to op-
timally plan for pick and replenishment
waves without negatively impacting on
the warehouse flows,” says Ettienne
Meyburgh, general manager – KZN
region and automation, APC Storage
Solutions SA.
APC provided the first block of 30 m
wide, five levels high and 68 pallets
deep; and another block of 10 m wide,
four levels high and 20 pallets deep,
coupled with a world-class wifi radio
pallet shuttle system operating on the
FIFO (first in, first out) principle. The
installed pallet shuttle system is designed
to prevent or minimise damage to racking
units and to best control FIFO and batch
receive and dispatch operations. It also
boosts pallet load and unload rates and,
therefore, throughput rates. The pallet
shuttles move along special rails attached
to the racking, eliminating the need for
aisles as storing and extracting pallets is
achieved via remote control using wifi-
enabled tablets.
As the pallet shuttle has its own ‘intel-
ligence’ and electrical supply system, it is
able to stock pallets deep inside storage
tunnels, then retrieve and convey them
to the front of the tunnel. Its deep lane
storage and retrieval, with the ability to
transport various pallet sizes with weight
loads of up to 1 500 kg, and at speeds
reaching 1.3 m/s, adds to increased
productivity and enhances product safety.
Operator time is reduced by half, in/out
flow efficiency is retained and available
storage capacity is maximised.
In addition, overall efficiency improve-
ments are gained by safer pallet handling
(a 10 mm accuracy rate), electronic pal-
let length checks for optimal density stor-
age, and the fact that operators remain
outside of the tunnels.
The pallet shuttles have several safety
and control systems in place, which in-
clude incorporated electrical components
that allow autonomous displacements,
radio frequency commands transmitted
to the shuttle’s PLCs, an incorporated
emergency stop button, sensors to bring
the shuttle to a halt in the event of a
collision or if obstructions are detected