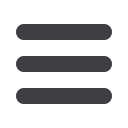

174
M
ARCH
2016
4-8 April 2016
Choosing the right coating
THERE are many different coatings
to choose from when it comes to
coating metal tubular items. The buyer
can choose liquid paints, tape-wrap,
sacrificial coatings, epoxy coatings or
powder coatings.
The powder coating market comprises
thermoset and thermoplastic powders,
with the former product group often
referred to as simply powder coatings.
Thermoplastic coating powders melt onto
the metal under the influence of heat and
then solidify into a coating. No reaction
takes place and they contain no reactive
ingredients.
Choosing the most appropriate
coating is dependent on the environment
the products will be exposed to.
If they will be exposed to water, acids
in soil, UV light, impacts, abrasion,
chemical attack, physical flexing,
temperature extremes or graffiti,
polyolefin (thermoplastic) coatings can
be considered. Thermoplastics are
flexible yet tough. They generally cannot
chip or crack, and adhere to the metal
well. Polyolefin thermoplastics
in particular adhere very well
to metal without the need for
a primer. They contain no
plasticisers, BPA or TGIC and
nothing can leach into the
environment or soil.
Polyolefin coatings are typically
supplied in powder form and can be
easily applied to tubular products by
electrostatic spray, flock spray or fluidised
bed dipping methods. They are of benefit
to manufacturers or coaters because
primers and chemical curing are not
required; they will not chip, crack or flake;
and no hazardous fumes are generated
on application.
The end customer has the reassurance
that coated assets will last for decades
with little to no maintenance costs,
and with no future environmental
liability. They are resistant to UV, wind
blown sand abrasion and sub-zero
temperatures, and can withstand the
rigours of urban life such as graffiti.
Plascoat states that its polyolefin coat-
ing powders are becoming increasingly
specified in the oil and gas, water and
street furniture markets, and are already
widely used to coat tubular products in
Europe, Asia, Australia, and South and
North America.
For the water industry, Plascoat PPA
571 Aqua is approved for contact with
potable water in the USA, UK, France,
Germany, Australia and New Zealand.
For oil and gas pipelines, Plascoat’s
products are approved by a range of
global pipe manufacturers. For street
furniture, Plascoat product PPA 571
is widely specified by many local
authorities.
Plascoat Systems Ltd
– UK
Email:
sales@plascoat.comWebsite:
www.plascoat.comA RANGE OF PRIMACY
Market leader in HSS and TCT circular saw blades for tube cutting.
TAKE THE CHANCE TO INCREASE YOUR PRODUCTIVITY!
MADE IN ITALY
CUTTING EXPERTS
ISO-9001:2008
certified company
Stark India Toolings (PVT) Ltd.
Andheri (East), Mumbai
Phone: +91 (0) 22 40661234
E-Mail:
total_tools@yahoo.co.inStark GmbH & Co.
Germany
Phone +49 (0) 7364 9608-0
E-Mail:
info@stark-werkzeuge.deStark Tools (Suzhou) CO., LTD.
P.R.China
Phone +86 (0) 512 58907826/28
E-Mail:
stark@starktools-cn.comStark Do Brasil Ltda
.
São Paulo - Sp - Brasil
Pabx +55 (0) 11 2721 6965
E-Mail:
starkbr@starkbr.com.brSTARK S.p.A.
Italy
Phone +39 0432 998811
E-mail:
info@starktools.com http://www.starktools.comPlascoat’s polyolefin coating powders are used in the oil
and gas, water and street furniture markets
S
t
a
n
d
n
o
.
16H09