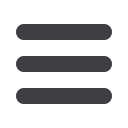

178
M
ARCH
2016
4-8 April 2016
Orbital saw blade for stainless steel tube mills
TUBEMASTER Stainless, a product
being introduced by Kinkelder, has
been developed for cutting stainless
steel tubes on orbital flying cut-off
machines.
Extensive testing has demonstrated
that TubeMaster Stainless saw blades
can cope with cutting speeds from 60 to
100m/min. Blade life of the TubeMaster
Stainless averages between 3.5m
2
at 60m/min and 1m
2
at 100m/min,
allowing high production output with
less downtime.
Production of stainless steel tubes is
often limited by the speed at which the
tube can be cut, typically around 2m/min
for large diameter tubes (Ø ≥200mm).
HSS saw blades are typically used for
this type of application, which results in
a limited maximum line speed. As burr-
free cutting of stainless steel usually
proves to be a challenge for TCT saw
blades, these have not been considered
as a reliable alternative.
The new TubeMaster Stainless
design derives from the Kinkelder
CX 4 concept. On a tube mill with a
two-blade orbital flying cut-off unit,
producing AISI 304L tubes of 323
x 4mm, it was demonstrated that a
cutting speed of 80-100m/min at a feed
rate of 0.05/0.1mm per tooth enables
a line speed of 10m/min. The blade
shows good cutting performance under
these conditions by cutting burr-free up
to 1m
2
per blade.
Under less aggressive conditions – a
cutting speed of 60m/min at a feed rate
of 0.035/0.05mm per tooth – burr-free
cutting up to 3.5m
2
per blade was shown.
With these cutting parameters, a line
speed of 6.7m/min is still possible. This
example shows a clear trade-off between
blade costs and production yield.
The value of the tube being produced
combined with the total cost structure
(saw blade costs, operating costs per
hour, total installation costs per hour)
defines which option to choose. Focusing
only on lowest blade price or cost per
m² cut-surface can lead to missing the
optimal economic conditions.
Kinkelder BV
– Netherlands
Fax: +31 316 58 22 17
Email:
info@kinkelder.nlWebsite:
www.kinkelder.comNon-destructive testing and coating solutions
THE Rosen Group, headquartered in
Stans, Switzerland, will participate at
Tube 2016, Germany, this year, where
it will present selected solutions to
challenges in various industries such
as pipe manufacturing, oil and gas and
mining.
Many challenges face these and
other industries. Tube and pipe
manufacturers, for example, must
ensure high quality standards during
the entire pipe manufacturing process.
Pipeline operators, on the other hand,
need to stay abreast of any threatening
conditions in their lines, such as
corrosion, ageing or other types of
damage.
The Rosen Group draws from its
decades of experience and extensive
know-how to develop customer-tailored
inspection and coating solutions to cope
with these issues.
Rosen’s industrial diagnostics divi-
sion delivers customer-operated, quality
control-driven diagnostic systems
for the pipe manufacturing industry
to ensure flawless manufacturing
processes.
All inspection systems are tailored
to the customer’s individual needs
and production process. The portfolio
comprises consulting, mechanical
engineering, automation, development
of testing technology, installation and
maintenance.
With their intelligent plastic solutions
division, Rosen delivers internal and
external coatings with outstanding
material properties for wear and
corrosion protection. Depending on
operating conditions, these coatings
can extend the life expectancy of
slurry, concentrate or tailings pipelines
by a factor of five to ten compared to
non-coated carbon-steel pipe spools.
The result is that shutdowns and
maintenance costs are minimised,
while the asset’s lifetime is significantly
extended.
Rosen
– Switzerland
Website:
www.rosen-group.comAutomated weld seam and full-body inspection system
S
t
a
n
d
n
o
.
7aB07
Newly developed connecting system
for coated pipes
S
t
a
n
d
n
o
.
6A52