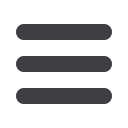

52
M
ARCH
2016
T E CHNOLOG Y
Bending production with BendingStudio 3.0
AICON 3D Systems has launched a
new version of the software platform
BendingStudio, offering new features to
facilitate daily work in bending production,
and with a new control concept.
In BendingStudio 3.0, user-friendliness
has been totally revised, with the aim of
a clearer structure and easier handling.
The set-up of inspection plans is now
separate from the measurements,
so the user sees only the information
that is relevant, and comparative
measurements become easier.
The set-up of new parts (eg creating
bending elements from CAD files)
is completely integrated into the
application ‘part editor’. This new
arrangement optimises the process of
measurement and analysis. The menu
structure of the different applications
has also been regrouped, so the user
will find all relevant process steps
neatly arranged.
BendingStudio 3.0 also offers
extended measurement options. Any
connected measuring device, such as
Aicon’s TubeInspect or MoveInspect,
only provides the measured centre line.
A special wizard guides the user through
the steps of the bending point model, and
the user can intervene when needed.
The analysis is usually automated,
but manual interference is now more
transparent and graphically supported. In
Reverse Engineering, different bending
radii can easily be taken account of.
In the new software, it is possible
to repeat analyses of a measurement
afterwards, making multiple measure-
ments easier. The user can either delete
measurementsorchangetheparameters
of the analysis. This is especially useful
in partial measurements, ie if the part
cannot be measured in a single step.
Larger components are measured by
overlapping repositioning section by
section, and the partial measurements
are then combined.
If the overall measurement is not
successful, new single measurements
are added, defective measurements
deleted or single measurements re-
evaluated with changed parameters.
This allows for a more effective
workflow, as the part does not have to
be completely re-measured in case of
errors.
The first version of BendingStudio
had its world premiere at Tube 2012
in Düsseldorf, Germany. Since then,
it has been continuously optimised.
BendingStudio connects all data and
processes around production of bent
parts, from production and process
planning to manufacturing and quality
control.
Holders of appropriate licences and a
valid software maintenance contract will
receive the new BendingStudio version
3.0 with the next software update.
Aicon 3D Systems GmbH
– Germany
Fax: +49 531 58 000 60
Email:
info@aicon.deWebsite:
www.aicon3d.deDouble order for ERW tube mills
FD Machinery has received orders for
two CNC-CFS (direct form square)
ERW tube mills from APL Apollo Tubes
of India. These mills are designed and
patented by FD Machinery and are fully
automated.
Making a size change takes only five
minutes and is done by simply entering
four parameters into the touchscreen.
The size range of the mills is 80x80
to 200x200mm square, with wall
thicknesses ranging from 3 to 10mm.
The tube length can be 4-8m and the mill
speed is 20-60m/min. All adjustments,
except welding and straightening, are
performed automatically and only one
set of tooling is required to produce the
mills’ entire size range.
The mills will be equipped with
automated strip entry sections
and automated bundling/strapping
machines. Only three operators will
be required to run an entire mill. The
addition of these mills is expected to
significantly increase APL’s production
capability.
FD Machinery has received enquiries
for its direct form square mill from US
and European tube producers. The
company also recently received an
order for a dual-cart flying cut-off from
APL. This cut-off will be used for tubes
with diameters of 12 to 50mm and wall
thicknesses of 1 to 3.2mm, and will
allow the mill to run at speeds up to
200m/min.
FD claims that its dual-cart cut-off
increases blade life by 30 per cent,
gives better end finishes, and reduces
blade changeover time compared to a
100m/min single-cart cut-off.
FD Machinery
– USA
Email:
sales@fdmachinery.comWebsite:
www.fdmachinery.comThe new BendingStudio 3.0 helps the user make fast fault detections