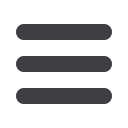

92
M
ARCH
2016
T E CHNOLOG Y
•
CONDATUB SL: Solubles for
rolled & welded tubes
•
COLLUBE: Reactive soaps
•
CONDATUB TFH: Drawing oils
Hall 10
Stand A52
Leader in the wire drawing lubricants market,
Condat now proposes its high level customer
support and 160 years’ expertise for the tube
forming market too.
LUBRICANTS
FOR STEEL TUBES
CONDAT -
104 av. F. Mistral - 38 670 Chasse-sur-Rhône - FRANCE
Tel. +33 (0)4 78 07 38 38 -
www.condat.fr-
wire@condat.frLooking for
distributors
worldwide
®
Passive thermography as
an in-line NDT method
THE use of an in-line non-destructive testing system offers
many advantages. For example, the mill can be stopped as
soon as problems occur and the amount of faulty tubes can
be reduced, resulting in the saving of scrap.
Based on the physical principles, the use of eddy current
systems for in-line testing is limited to the detection of
irregularities on the surface of a weld seam. Critical faults
such as cold welds, root forming problems and variations of
penetration depth or symmetry are not detectable by the use
of eddy current.
To detect these and other critical welding irregularities, as
well as process disturbances, HKS Prozesstechnik began
to develop the ThermoProfilScanner thermo line camera
for welding applications in 2007. This robust, compact and
lens-free IR-measuring device is placed directly behind the
welding point and measures the temperature in a line with a
scan frequency up to 400Hz.
The constantly captured thermo profiles across the welding
seam are evaluated and checked against the maximum
temperature, the width of temperature zone, symmetry, profile
position and form differences. Irregularities of the weld seam
and process disturbances are detected due to the incorrect
heat input and/or disturbed heat distribution. Even pressure
changes of the forming rolls, damaged forming rolls and worn
out bearings inside a tube mill can be detected.
Since the system was developed with several protection
mechanisms it can be used in arc-, laser beam- and electron
beam-welding processes. Brazing and electric resistance
welding applications are also possible.
In the example illustrated, a tube with a cold weld was
welded inside an HF-ERW (HFI) mill. With a welding speed
up to 600fpm the fault was only detectable by using an in-
line system. By evaluating the emitted thermal radiation the
welding irregularity is detected and becomes visible in the
thermogram as well as in the parameter curves. Based on
the physical effects, the faulty part was not detected with an
eddy current system.
HKS Prozesstechnik GmbH
– Germany
Email:
sales@hks-prozesstechnik.deWebsite:
www.hks-prozesstechnik.deThermoProfilScanner detects cold weld (seam picture, thermogram
and calculated parameter curves)