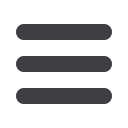

96
M
ARCH
2016
T E CHNOLOG Y
Engineering custom solutions
FOR metal forming equipment manu-
facturer Formtek, Inc, giving customers
the best tools to perform their work
means combining durable, innovative
and proven technologies into the ideal
machine line.
However, it is rare to find a single
provider for every equipment solution.
Formtek states that it has adapted to
meet customers’ highest standards by
allowing them to source the components
of their equipment line from preferred
companies. Formtek’s tube mill is one of
these custom manufacturing solutions.
After dealing with repeated delays
on shipments for tubing, a producer of
industrial cable spools decided to bring
the tube manufacturing in-house. The
customer contacted the Formtek Group
to find a machine solution that would
meet their specifications, keep costs
low, and improve overall profitability.
The customer was seeking a full
production line system, with a tube mill
at its core, that would allow it to make
square and rectangle shapes of ¾"
to 3" OD, with wall thickness of up to
0.134". Formtek developed a plan for
the full production line, including what
equipment would be necessary for the
process.
Although Formtek could provide the
tube mill, some of the line equipment
fell outside its manufacturing scope. For
the additional equipment, the customer
was directed to appropriate resources to
purchase it directly and save money.
Brian Kopack, the Formtek engineer
who worked with the client, said, “The
way we see it, they’re coming to us for a
solution. If we can point them in the right
direction and keep their costs low, we’re
going to do that. What’s more, once they
had the equipment they needed, our
objective was to stay on and advise them
as to the best line set-up possible.”
In addition to an optimised production
line, the customer’s new tube mill
had a number of
features that would
make
production
simpler. To improve
changeover times,
the mill’s rafting
system incorporated
the weld box and
turkshead rolls, so
a full swap could
be performed in
one
manoeuvre.
Another
feature
involved developing
a custom bead chopping system
integrated into the scarfing process,
which kept operators from having to
interact with the bead – an activity
that is typically high-risk. The mill also
has a seam rotation stand included for
projects that require specific weld seam
positioning.
All of these capabilities were
described at length during the initial
quoting process with the customer, who
decided to include the features.
“Every enquiry involves exploration
and discussion. It’s the only way to
deliver the most satisfying solution,”
said Mr Kopack. “Even when customers
come forward with their own designs
in mind, we see how we can expand
on those and present them with all
the options. For example, we took this
customer on a tour to see a couple of
our different mill solutions in action.
If there’s a way we can make their
business safer or more profitable, they
deserve to hear that.”
To ensure customers are prepared
to get the most out of their machinery,
Formtek takeson full projectmanagement
responsibility, includes advising on
equipment components, ensuring they
all fit together, matching pass lines,
coordinating installation, and reviewing
operating directions after delivery.
Formtek, Inc
– USA
Fax: +1 216 292 4898
Email:
sales@formtekgroup.comWebsite:
www.formtekgroup.comCladding system from Polysoude
FOR its latest system Polysoude has
built on the main principle of hot wire
technology, which is the preheating
of filler material in order to reduce
the quantity of energy taken from the
electrical arc, required to melt the filler,
thereby assuring increased productivity
of cladding speed and deposition rate.
In addition to the pre-heated filler wire
TIGer incorporates a unique system
of two tungsten electrodes in tandem
configuration.
This allows the ignition of two
electrical arcs, which, by way of mutual
attraction, combine to convey a single
heat source. This single heat source
has a lower arc pressure than in classic
tandem configurations, yet it is capable
of reaching much higher cladding
speeds and deposition rates than the
standard TIG/GMAW HW process.
The requirements of this field are not
easily met. However, the TIGer aims
to rise to the challenge of achieving
improved productivity by increasing
deposition rate and cladding speed,
while keeping the lowest possible
dilution in order to reduce the number of
layers and thereby optimise production
times and costs of consumables.
The characteristics of the TIGer
system mean that it is capable of
enhanced process applications in
cladding, being suited to horizontal
and vertical cladding, both inside and
outside components.
The TIGer has cladding speeds
and deposit rates capable of reaching
950mm/min with a deposit rate from
2.7 to 5.8kg/h. It also offers conclusive
results from adherence checks on
cladded layers and offers excellent
outcomes from inter-granular corrosion
tests and positive outcomes from
chemical analysis.
Polysoude
– France
Website:
www.polysoude.comCustom solutions from Formtek