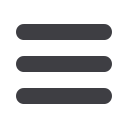

ELECTRICAL PROTECTION + SAFETY
References
[1] SANS10199. 2010. The Design and installation of earth electrodes.
[2] IEC 62305-3. 2006. Protection against lightning – Part 3: Physical
damage to structures and life hazard.
[3] SANS/IEC 62651. 2013. Nuclear power plants - In-
strumentation important to safety - Thermocouples:
characteristics and test methods.
ROUND UP
Custom built E Houses… cost effective alternatives
Custom built E-Houses offer a rapid and far
more cost effective alternative to the build-
ing of brick and mortar substations, and
this is especially true in an underground
application.This is one of the reasons why
Zibulo Colliery contracted
Shaw Controls
,
a division of
Zest WEG
Manufacturing, to
design and manufacture an E-House for its
operation in the Mpumalanga coalfields.
Containerised electrical control installations
in underground applications are not new.
Bevan Richards, Chief Operations Officer of
Shaw Controls, says the concept was first
used during the sinking of many of South
Africa’s gold mining vertical shafts when
ISO marine containers were equipped with
mimic panels and other ancillary equipment.
“However, the evolution and devel-
opment of pre-manufactured electrical
substations or E-Houses has opened up
numerous possibilities including the ability
to completely customise the unit accord-
ing to process and plant requirements,”
Richards explains. Specifically designed
for this underground application in a coal
mine, the E-House was designed with sev-
eral specific parameters taking precedence.
Underground height restrictions meant that
the structure itself had to be lower than
usual but would still need to accommodate
all necessary electrical infrastructure and
allow for sufficient headroom for cooling.
Richards says it is testimony to Shaw
Controls’ mechanical design capability that
its engineers were able to design such a
low profile steel structure that could house
all the equipment and still maintain the
requisite internal clearances.
Another important criteria that had to bemet
was the voltage being used on the mine.The
majority of mines use 525 Volts, but in the
instance of Zibulo Colliery the voltage being
used is 1 000Volts.This required special de-
sign work on both the Motor Control Centre
(MCC) and theVariable Speed Drive (VSD) to
ensure safe operation at 1 000Volts.
Enquiries: Kirsten Larkan.Tel. +27 (0) 11 723
6000 or email
marketing@zestweg.comELECTRICAL PROTECTION + SAFETY
Trevor Manas started his lightning protection career at
Pontins in 1991. After spending some years in sales,
he was promoted to the position of director in 1996, in
charge of ensuring the company`s compliance with the
earthing and lightning protection codes of practice. In
1999, Trevor became the managing director of Pontins.
In 2013, Pontins formed a partnership with DEHN Africa. Enquiries: Email
trevor@pontins.co.za- Proper site assessments must be carried out including the carry-
ing out of various soil resistivity surveys, appraisal of the soil`s
corrosiveness and the determination of the various external
factors that can cause corrosion of the earthing and lightning
protection components.
- Quality engineering and properly designed protection
systems must be employed taking into account the
various corrosive elements that may exist on the
site and the correct combination of the various
LPS conductors.
- Additional protectionmeasures such as the use
of anti-corrosive tape on the belowground con-
nections should be installed on sites that could
be corrosive and where clamped or crimped
below ground connections exist.
- Bi-metallic joints must be installed when two dis-
similar metals are joined.
- Copper parts should never be installed above galvanised
or aluminium parts unless those parts are provided with protec-
tion against corrosion. Extremely fine particles are shed by copper
parts which result in severe corrosive damage to galvanised parts
even where the copper and galvanized parts are not in direct
contact.
- LPS should be constructed of corrosion-resistant materials such
as copper, aluminium, stainless steel and galvanised steel.
Electricity+Control
April ‘16
20