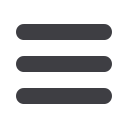

ROUND UP
NEW utility-scale solar inverter testing laboratory
A new multimillion dollar facility designed to test high power central
photovoltaic (PV) inverters has been opened in Helsinki.The new labo-
ratory features a unique, large climate chamber capable of full power
electrical testing in conditions simulating the arctic tundra to an equato-
rial rainforest. In addition, full verification and grid code requirements
testing enable ABB to develop larger, more powerful inverters to meet
the developing customer and industry trends. The laboratory supports
testing and verification of inverters for safe operation, endurance in a
wide range of climatic conditions, compatibility to the most demanding
renewables-specific grid code requirements, and to measure and test
harmonics and grid interactions.
Marc Gomez, Global Product GroupManager for solar inverters at
ABB
states: “Our customers are asking for more powerful central inverters.
They want to maximise their return on investment and connect more
incoming PV power to one inverter.With this lab, we are able to test new
inverter concepts, under varying weather conditions, and that allows us to
deliver new innovation to our customers and ensure we lead the market.”
Climate testing can last several weeks for the equipment under test.
Powered by a dc supply, the inverters are run at varying power levels
with different simulated weather conditions to test inverter reliability.
The climate chamber allows for accelerated product testing, important
when the inverters are typically expected to operate for over 20 years.
The climate chamber can vary temperatures from as low as -40°C to as
high as +100°C, and relative humidity levels up to 95%.
Enquiries: Paul Louw.Tel. +27 (0) 10 202 5916 or
A5 UMC 100.3 E&C 2016.indd 1
3/29/2016 1:12:26 PM
TRANSFORMERS + SUBSTATIONS
41
April ‘16
Electricity+Control