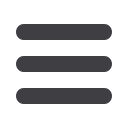

58
Wire & Cable ASIA – March/April 2015
www.read-wca.comA single straight filament located at the axis centre of the
die can maintain uniform temperature on the surface of
the bore of the drawing die during the deposition process.
A DC bias is applied between the filament and the drawing
die substrate so as to enhance the diamond nucleation
density.
3 Characterisation and discussion of
nanocrystalline diamond composite
coating dies (nano-dies)
Figures 2a
and
2b
show the surface morphology of
conventional multi-crystalline and nanocrystalline diamond
coatings. For conventional multi-crystalline diamond,
as shown in
Figure 2a
, the film displays a well-faceted
microcrystalline diamond surface with grain size ranging
from 2 to 4μm. The surface is very rough and consists of
a combination of {111
}
and {110} facets. For nanocrystalline
diamond, as shown in
Figure 2b
, the film appears very
dense with a fine-grained morphology (grain size about
50nm). The surface morphology is non-faceted and much
smoother than multi-crystalline diamond films.
Figure 3
shows the Raman spectrum of the composite
coatings of multi-crystalline diamond film and nano-
crystalline diamond film. For conventional multi-crystalline
diamond films, the only sharp characteristic peak
for diamond (sp
3
carbon) appears at 1,332cm
-1
. For
nanocrystalline diamond films, a characteristic peak for
diamond (sp
3
carbon) appears near 1,339cm
-1
. And a
broad peak near 1,580cm
-1
corresponds to amorphous
carbon or non-diamond carbon (sp
2
carbon). It can be
inferred that the conventional multi-crystalline diamond
film contains much less non-diamond component.
For nanocrystalline diamond, the diamond band at
1,332cm
-1
is significantly broadened, and Raman
scattering intensity near the 1,560cm
-1
region is
pronounced. Broadening of the diamond band is a result
of decreasing the grain size to the nanometer scale, and
the presence of scattering intensity at 1,560cm
-1
is due to
increasing graphite-like or amorphous carbon sp
2
-bonded
components at the grain boundaries in films. Raman
scattering is 50~60 times higher for sp
2
-bonded carbon
compared to sp
3
-bonded carbon, hence the diamond
component dominates in films. The Raman spectrum
of the nanocrystalline diamond film in
Figure 3
can be
regarded as the representation of the surface of the
composite diamond film because the Raman spectrum
reveals the structure of the top layer of the film.
The surface profiles of conventional multi-crystalline
coating and nanocrystalline diamond composite coating
were tested with the same thickness at five sampling
sites with surface profilometer, and the results of the
surface roughness (Ra) were 309.64nm and 104.71nm,
respectively. By comparison, Ra of the nanocrystalline
diamond composite coating could reach 30nm or even
lower after mechanical polishing.
According to the characterisation and analysis, the
nanocrystalline diamond coating has a smooth surface
with a grain size of about 50nm, which is much smaller
than conventional multi-crystalline diamond coatings.
This is advantageous to the surface polishing of diamond
coatings. Therefore, nanocrystalline diamond composite
coatings dies (nano-dies) can easily be fabricated,
see
Figure 4
(with die casing), to meet the requirements
of both excellent wear resistance, very high finish and low
friction with aluminium.
4 Application tests of nano-dies for
aluminium wire drawing
4.1 Conventional application
tests of nano-dies for
aluminium wire drawing
We prepared nano-dies with various specifications
(bore diameter smaller than 4mm) for aluminium wire
drawing, using the above nanocrystalline diamond
composite coatings technology and subsequent polishing
technology. According to practical aluminium enamelled
wire and aluminium wire drawing tests performed on the
production lines of customers in China, nanocrystalline
diamond composite coatings show very good adhesion
performance, wear resistance and much lower surface
friction. The nano-dies showed a die life improvement by
a factor of about 10 to 25, when drawing speed was about
15m/second, so it can not only save cost of drawing die
itself, but also largely reduce change-over time (only 4%
to 10% of previous process) and dramatically increase
productivity. Because the friction coefficient between
diamond coating of nano-dies and aluminium conductor is
so small (only about 0.09), use of nano-dies can obviously
improve the surface finish of drawn products and avoid
aluminium galling on drawing dies. The super wear
resistance of the diamond coating of nano-dies yields
❍
❍
Figure 5
:
The water lubricating application in Al-plastics
compound pipe drawing process with nano-dies and
appearance of the aluminium product