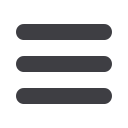
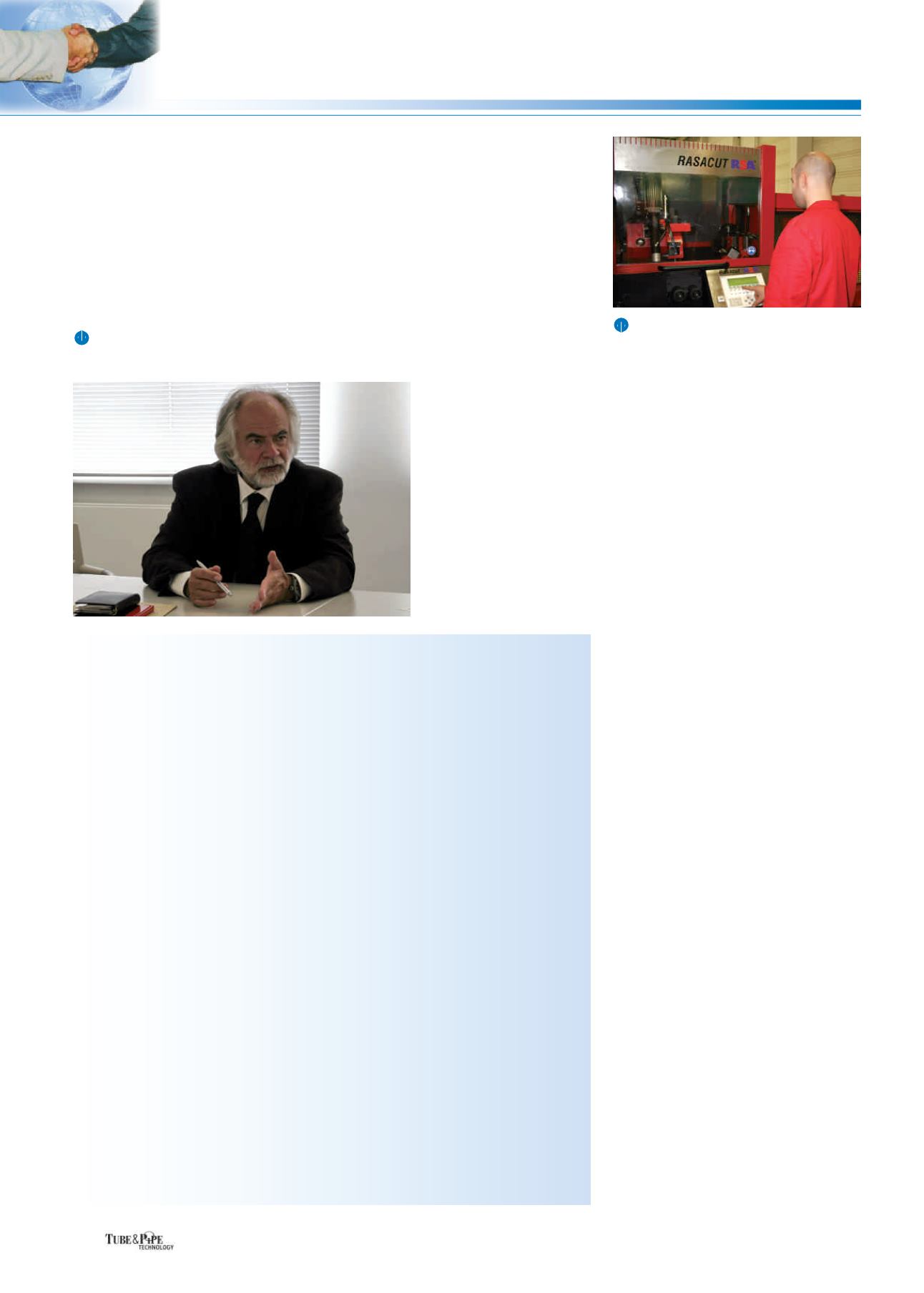
10
N
ovember
/D
ecember
2007
Industry
News
RSA, Germany, has reported a 160 per cent
increase in orders already for 2007, based
on only the first six months. The company
is holding course to achieve its envisaged
sales growth in double figures.
The company is a specialist in machines
and technology for the sawing of tubes,
sections, and solid bars. According to
business manager, Dipl-Ing Rainer Schmidt,
this development is not only the result of
the upward economic trend. He says:
“The
reason why we are growing above the
average of the branch is mainly due to our
product strategy.”
RSA has launched four new sawing
concepts during the period of 2006 to
mid-2007. These
have
been further developed
from existing modules, in
addition to completely new
developments. One of the
new developments concerns
a saw that meets the special
requirements of the steel
trade and the pre-production
of forged products.
The Rasacut XXL is used
to cut tubes with a wall
thickness of up to 15mm and
diameters of up to 170mm.
According to the company,
this results in a cutting time
reduction of up to 90 per cent
compared to up-to-date band saws – while
the quality of the cut surface is significantly
improved.
For stainless steel processors, RSA
provides the Rasacut TC saw which can cut
thin-walled tubes of a wall thickness from
0.4mm with surface protection and without
deformation. For the main customers of the
components suppliers to the automotive
industry, RSA has developed two sawing
centres for specific applications.
One machine is designed for the production
of vehicle lines from 0.6mm diameter that
are deburred or chamfered on both ends
and subsequently cleaned on the inside
and outside with a very high degree of
purity. A second specialized sawing centre
concerns the high precision cutting, facing,
chamfering, and checking of solid bars to
be further processed into motor shafts.
Though there is a good demand in Germany,
RSA sees an international market potential
for these state-of-the-art installations,
especially in eastern Europe.
According to Rainer Schmidt, the increase
in orders does not result in delivery delays:
“Though our delivery times are shorter than
the usual delivery times in the market, we
are aiming at even significantly reduced
delivery times. We are able to meet our
delivery times, because we have allowed
for the growth – and as a result extended
the production capacities and the resources
of the after-sales service.”
RSA GmbH & Co KG
– Germany
Fax
: +49 2351 995-300
:
pr@rsa.deWebsite
:
www.rsa.deRSA Cutting & Deburring
Systems Ltd
– UK
Fax
: +44 1952 580511
:
rsa.gb@rsa.dePlymouth Tube acquires Trent Tube
from Crucible Materials
Plymouth Tube Company has acquired Trent Tube from Crucible Materials Corp. The
purchase includes the Trentweld Plant (East Troy, WI) and the Trent Processing Plant
(Chicago, IL). Previously, Plymouth Tube acquired the Cold Work Anneal plant (also
East Troy, WI) from Crucible in 2005.
Mr Don Van Pelt Jr, president of Plymouth Tube, remarks that
“We are excited by the
addition of our new offerings to the market and look forward to promoting the strengths
of these new Plymouth facilities.”
Trent Tube’s Trentweld Plant produces
1
/
8
" to 4" diameter welded and welded and
drawn stainless steel tubing including nickel and high alloys for a variety of applications.
Primary products include mechanical, air cylinder, electropolished tubing, and speciality
tubing products such as tubing for aircraft, sanitary, pharmaceutical, high purity, and
nuclear applications.
The Trent processing plant provides slit and edged stainless steel and nickel alloy coils
(0.010" to 135" thick x 0.375" to 48" wide). Customers served by Plymouth include the
Trent Weld plant as well as a broad base of other steel processors.
Plymouth Tube Company is a privately-held, family-owned global supplier of speciality
carbon, alloy, stainless steel, and nickel alloy tubing. In addition, Plymouth produces
steel, nickel alloy and titanium extruded shapes and cold drawn shapes. Plymouth Tube
is headquartered in Warrenville, Illinois with 10 plants in the US, and sales representation
around the world.
Plymouth Tube Company
– USA
Fax
: +1 630 393 3551
Website
:
www.plymouth.com›
A sawing centre designed for the special
requirements of components suppliers to the
automotive industry: this involves sawing, facing,
chamfering, and 100 per cent control of solid bars
as a pre-product for shafts
fi
Dipl-Ing Rainer Schmidt, business manager of RSA, considers the
product strategy of the ‘customized modules’ as the deciding factor
for the good course of the company
RSA reports an order increase of 160 per cent