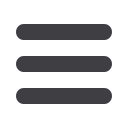

42
Tube Products International January 2016
www.read-tpi.comproducts & developments
Welding equipment and techniques
for extended network documentation
The main goal of a grid owner is the
reliable and secure supply of water
or gas to its customers. This can be
achieved by the use of high-quality
piping components, proper installation
and operation by qualified personnel.
To ensure the water and gas supply,
grid owners often maintain electronic
welding protocols. They contain the
welding parameters, product-specific
data of the respective PE components
(traceabillity code according to ISO
12176-4), details about the installer
(installer badge according to ISO 12176-
3), and additional information about the
site, which are entered either manually
or via barcode into the welding device.
There is often no further evidence about
the installation quality. Documentation
after installation may be missing, and
different documents will be stored in
different systems.
Modern network documentation for PE
piping is not limited to the provision of
electronic welding records according
to standards. It claims to depict the
entire life cycle of all components of
a piping system from manufacturing
to installation and operation. New
technologies ensure the safe and central
storage of the documentation, while the
information is available any time and
anywhere.
Further data can be added at all
project stages. The grid owner can
extract analyses about the construction
progress as well as the involved
installation companies and used
components. Welding records and
pictures taken during installation are
available as evidence for the quality.
GF Piping Systems has used QR
codes for some time to identify
ELGEF electrofusion fittings. In the
manufacturing process each fitting is
provided with an individual QR code for
unique identification. During production
the record is provided with current and
specific data.
The code enables use of the GF Trace
App on a smartphone. This service
helps to secure the installation quality
and support the documentation of the
piping components. When using the
new electrofusion devices of the MSA 4
family on site, the QR codes can be read
with 2D scanners. The code contains
information about the trace and welding
barcodes, both stored in the welding
record.
The GF Trace App allows an operator
to match and save data to existing
manufacturing information of specific
QR codes: pictures, videos, site name,
order number, welder ID, welding number
and accurate GPS coordinates
– everything deposited into the
GF Web T & A (tracking and
analysis) platform. The wireless
scanner of the MSA 4.1 is a PDA,
and already prepared for the GF
Trace App, so smartphones are
not required at the site.
The protocols extracted from
the welding device are filtered, edited
and transferred with an evaluation
application to the GF Web T & A
database by the installation company.
According to the authorisation, a quality
check or analysis of the components
can be made during or shortly after
installation on the web platform.
The system is also suitable for welding
devices without a 2D scanner. The
protocol format CSV enables the
import of protocols from other devices
into the evaluation software. On the
web platform, unique QR codes can
be generated for the identification of
components that do not yet have them.
This allows the application to be used for
competitive or mechanical components
such as valves.
After installation the data set can be
extended with results from pressure
tests or protocols of non-destructive
testing. Maintenance cycles for valves
and fittings can be deposited in the
system to simplify network maintenance.
This application completes network
documentation, and keeps it up to
date and available online, allowing grid
owners to ensure compliance with their
specifications.
GF Piping Systems Ltd
– Switzerland
info.ps@georgfischer.com www.gfps.comMSA 4.1 electrofusion unit with full
traceability and wireless scanner