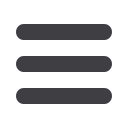

50
Tube Products International January 2016
www.read-tpi.comSteel tubes and pipe
Setting a standard in hydraulic and
instrumentation tubing
As a producer of steels for over 150
years, Sandvik maintains its position
at the forefront of research and new
product development.
“Whether you’re operating an oil rig
or a petrochemical plant, the need to
boost output without sacrificing safety
is ever-present,” explained James
Doughty, Sandvik sales manager, MENA
region, for tube, core and standard
products.
“In the big scheme of things, your
choice of hydraulic and instrumentation
(H&I) tubing might not seem critical, but
it does make a difference in eliminating
risks. No unscheduled downtime, no
leaks, no accidents, and immediate
support if you need it. It’s what we call
‘The Sandvik Peace of Mind Standard’.”
International standards such as ASTM
and EN certifications help guide
distributors and their buyers. The
challenge is that many of these standards
only provide recommendations for
minimum or maximum levels.
“It really is important to ask yourself
whether your supplier is providing the
optimum quality for your particular
application, even if the quality supplied
is technically within the standard,”
commented Mr Doughty.
As an example, Sandvik 3R60 H&I
tubing has a minimum 2.5 per cent Mo
content for higher corrosion resistance,
compared to the minimum ASTM
standard of 2 per cent Mo. Sandvik
looks beyond the minimum standard
for H&I tubing, achieving higher pitting
corrosion resistance, or PRE numbers.
“When customers invest in their
assets, they don’t want unscheduled
maintenance and ultimately production
stops, the cost of which can run into
millions,” added Mr Doughty.
“Our aim is provide producers with the
lightest, strongest, most reliable H&I
tubing possible. It is our consistent
material quality and tight dimensional
controls from batch to batch that
ensure leak tight seals and operational
longevity with reduced operational and
lifecycle costs – something we can
clearly demonstrate.”
The company stresses the importance
for customers to source their H&I tubing
from a recognised Sandvik distributor,
to ensure they receive the expected
product quality.
Sandvik Materials Technology
–
Sweden
www.smt.sandvik.comSandvik hydraulic and instrumentation tubing
Tata Steel’s new welded product range
Tata Steel has expanded on its new
range of welded line pipe. Last summer,
the company successfully delivered
diameter submerged arc welded
longitudinal (DSAWL) pipe through
reeling method in the North Sea. The
size range extension has expanded
the range further, with the company
producing a range of new X65 sizes,
with a wall thickness of up to 38.1mm
and a diameter up to 559mm.
In doing so, the company can now offer
traditionally seamless pipe sizes in a
welded form, the benefits of which include
a decreased lead time in customer orders
and improved fit up and weldability.
The new products have already been
deployed in the North Sea and in deep
water projects in the Gulf of Mexico.
Martin Connelly, technical manager, Tata
Steel, said, “This development marks
another huge success for Tata Steel
and for our customers. Our team has
worked extremely hard to develop
this new generation of welded pipe
which will contribute to a lower cost of
operation and ownership of assets for
our customers.
“We have invested heavily in research,
development and innovation and with
the aid of our state-of-the-art finite
element (FE) modelling and tooling
programme this project has come to
fruition. A recent installation of 140km
of 457mm OD x 28.6mm wall thickness
within deep water off the Gulf of Mexico
was produced in such a way that it
was able to meet the manufactured
requirements of DN OS-F101, should a
reel installation be considered.”
Tata Steel recently invested in welding
control technologies within its 42" UOE
mill, including weld condition monitoring
and digital front-end control of the SAWL
welding process. Investment was also
made to ensure the ovality of the pipe is
as perfect as possible to the expander,
with the business reviewing the full
forming process including tooling design
and a fully validated FE model.
Tata Steel Europe Ltd
– UK
feedback@tatasteel.com www.tatasteeleurope.com