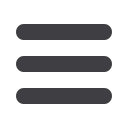

January 2017 TUBE PRODUCTS INTERNATIONAL
53
Welding technology
Weld backing tape for weld purging
It is important when welding metals
such as stainless steel, titanium and
zirconium that the welding zone is
purged of oxygen even as low as ten
parts per million (ppm) before, during
and immediately after welding, in order
to achieve a clean, oxide-free, zero-
colour weld.
During a recent trip to South America,
weld purging experts from Huntingdon
Fusion Techniques (HFT) were
supporting their exclusive distributor
and local customers when a discovery
was made concerning the use of the
company’s Argweld
®
Backing Tape™.
A customer showed how the use of his
former ceramic backing tiles and the
tiny space available for the weld root
formation prevented adequate argon
flow and caused the welding arc to blow
back at the welder.
Luke Keane, distributor support for HFT,
explained, “Ceramic backing tiles are
designed for submerged arc welding
where oxidation is prevented by powder
as opposed to argon, so the customers
were using the wrong product for
GTAW/TIG welding. A demonstration
of Argweld Backing Tape followed,
which allowed the argon to flow freely,
eliminating the blow back of the arc that
was happening previously and enabling
the welders to produce a perfect root
weld.”
Huntingdon Fusion Techniques Weld
Backing Tape™ comprises a 75mm (3")
wide aluminium adhesive tape backing
strip, in the centre of which is a 25mm
(1") wide band of woven glass fibre
matting.
Once the tape is positioned
with the glass fibre matting
under the centre of the weld
joint, the welders can start
their arc.
The welding torch argon
flow has plenty of space to
move between the pores of
the matting, which allows
the welding arc to stabilise
and start forming the weld
root.
Measured by a Weld Purge
Monitor
®
, all contaminating
oxygen below 100 parts per
million (ppm) is removed and
the stainless steel weld root
is completed successfully,
with the molten metal being
cast onto the fibre glass with
excellent side wall fusion
and under-bead profile.
The customer was said to
be enthusiastic about the
clean, metallurgically sound,
non-oxidised weld, and
placed a large order for Weld Backing
Tape for immediate delivery.
Huntingdon Fusion Techniques
– UK
hft@huntingdonfusion.com www.huntingdonfusion.comGas flow using API sampling probe
Finished weld
New welding machine for HDPE pipe
Delta 1000 Trailer is a self-aligning
fusion machine suitable for welding
thermoplastic pipes for the transport
of water, gas and other fluids under
pressure, up to Ø 1,000mm (36"
IPS/DIPS). The machine can fuse
pipes according to the ISO 21307
High Pressure standard, enhancing
productivity and allowing a claimed
60 per cent time saving.
The machine body is mounted on a
four-wheeled chassis, with two steering
wheels and a safety brake, and is easily
removable for working in tight spaces.
Steel hydraulic clamping with fast-lock-
ing inserts allows placing and removal
of inserts in seconds. A self-detaching
device helps remove the heating plate
during the welding procedure.
An on-board hydraulic electric facer is
equipped with a safety microswitch to
prevent accidental starts, and a thermal
circuit breaker protects the motor.
The PTFE-coated hydraulic heating plate
is supplied with a high-temperature-
proof bag, to prevent the heating
element from being scratched.
The Easy Life control panel, with a large
graphic display and GPS traceability, is
removable from the machine body to
enable welding from outside the ditch.
This allows the operator to program
and pilot the welding cycle in an easy,
fast and intuitive way. A data-logging
system is included, to store full welding
data, downloadable through a USB port
straight into PDF files. The Easy Life
system has the capability store up to
4,000 joint reports.
The Delta 1000 Trailer allows easy
welding of fittings such as elbows,
tees, Y-branches and stub flanges.
Accessories available on request include
clamp inserts from Ø 335 to 900mm, a
trolley, a tool for flange necks, a kit for
in-ditch use, and a hoist.
Ritmo SpA
– Italy
www.ritmo.it