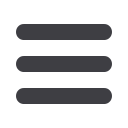

T
echnology
U
pdate
48
M
ay
2010
www.read-tpt.com›
ZUMBACH systems in the steel and metal
industry are used for manufacturing hot and
cold rolled products and in cold processes
for semi-finished products. Typical areas
where Zumbach systems are used are hot
rolling mills for wire steel rod, profiles and
seamless pipes, for the manufacture of
welded pipes, test stands (NDT) as well as
all cold processes, like peeling, grinding,
straightening and polishing.
Zumbach claims its products offer closer
tolerances (1/2, 1/4 DIN), zero fault, quality
control, higher productivity, faster start up,
less down time and less manpower.
It says its Steelmaster gauges and
systems help fulfil the high requirements
of the market. Steelmaster systems are
based on the latest technology and on
the experience with close to 300 units in
hot rolling and similar processes and they
are backed by many thousand ODAC
®
scanners, operating in cold processes.
The Steelmaster processor is the
brains of the system. It processes the
measuring data, communicates with the
plant network and provides the operator
with self-explanatory displays and key data.
The process transparency is dramatically
improved, especially if multiple measuring
heads are installed.
Steelmaster gauges offer a number of
advantages for easy integration, dependable
operation and data processing and display:
hi-tech laser scanners with top accuracy;
up to 6,000 measurements/s (1,000 per
scanner); compact industrial PC with
highest working reliability; highly developed
software; sophisticated mechanics and
protection system; and close to zero
maintenance.
The Profilemaster offers accurate in-line
profile measurement using light section
principle and machine vision.
One or up to six laser/camera modules
measure the cross-section of the moving
profile. A powerful PC-based processor
adds the partial pictures of the cameras
made up of straight lines and radii together
to yield the momentary cross-section of
the profile.
All relevant dimensions such as width,
height, angle and radii are added together
to form the full cross-sectional picture. The
nominal values for the profile can be directly
imported from the CAD construction (as
DXF file), which allows easy and problem-
free programming. Changes in speed and
twist within normal limits have no effect on
the measurement.
When designing the system, concen-
tration was focused on the most suitable
solution in terms of price/performance ratio
for the application. Due to the modularity of
the Profilemaster system this goal could be
achieved.
The combination of one to six laser/
camera modules allows the measurement
of virtually all shapes, achieving an optimal
measurement result with the smallest
possible number of laser/camera modules.
The Odac Trio system is based on
Zumbach’s previous experience of problems
faced in the industry, gained over many
years of designing and manufacturing optical
diameter gauges. The measuring heads
features three integrated measurement axes;
conventional two-axis instruments with laser
or CCD can only provide approximate values
for min. OD, max. OD and ovality. The mean
value (X+Y/2) is influenced by the orientation
of the product ovality within the measuring
field.
Zumbach Electronic AG
– Switzerland
Fax: +41 32 356 04 30
Website:
www.zumbach.comNon-contact in-line dimension
measurement for tubes
ODAC
®
Trio Laser
diameter measuring head
The Profilemaster
®
measuring unit (heavy duty and fully protected
version for harsh environments with four laser/camera modules)