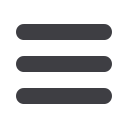

62
Tube Products International July 2010
www.read-tpi.comTianjin Pipe Corporation (TPCO) placed another order
for a RD660 HF pipe welding plant – the world’s largest
continuous pipe welding plant by its manufacturer’s
account. This plant serves to produce high-strength oil
field and line pipes complying with API standards, as
well as pipes for the construction sector with round,
rectangular and square cross-sections in line with DIN
10219. Round pipe dimensions here range from 244.5
to 660.4mm diameter, with wall thicknesses between 4
and 22.2mm. TPCO also awarded SMS with an order for
a RD355 HF pipe welding line that was commissioned in
late 2009. The two lines running at TPCO’s site will have
a joint annual output of 450,000 tons.
JSC Chelyabinsk (ChTPZ Group) in Russia has built a
new large pipe plant with an annual capacity of 600,000
tons for manufacturing longitudinally welded steel pipes
with diameters of 508 to 1,422mm, wall thicknesses of
up to 45mm, lengths of up to 18.3m and steel grades
of maximum K80. It is scheduled for commissioning in
2009 at the Chelyabinsk site in South Ural and will be
among the most modern of its kind in the world. The
pipes produced in Chelyabinsk will be joined to form
pipelines for oil and gas.
The pipe plant features two pipe forming presses: one
18.3m press and one 12.2m press. The 18.3m long
pipes offer a benefit in terms of lower pipe laying costs
because there are fewer welding seams required to join
the pipes compared to shorter pipes. By way of contrast,
the shorter pipes can also be produced with extremely
high wall thicknesses, despite their small diameters, and
are therefore especially well suited for offshore pipelines,
where they have to resist higher pressure.
Summer 2009 saw Zhongyou BSS Petropipe Co Ltd
commission a large pipe plant supplied by SMS to
Qinhuangdao, about 300km east of Beijing, China. The
new plant, with an annual capacity of up to 150,000 tons,
is thought to be the most modern of its kind in China. It
will be used to make longitudinally welded steel pipes
of 508 to 1,422mm diameter, with wall thicknesses up
to 40mm, lengths of up to 12.2m, and grades up to
X100. One of the decisive factors for placing the order
with SMS were the benefits offered by the JCO
®
pipe
forming press as the principal plant component.
By the firm’s own accounts, the JCO process developed
by SMS Meer has become the global standard because
it offers more flexibility, plus high quality and lower
investment costs than other processes. Over the past
few years it has been introduced at many large diameter
pipe plants and is considered the most suitable process
for producing even small pipe diameters with high
wall thicknesses. This means that the market segment
offshore pipelines can also now be served.
The commissioned line is suited to the production of
pipes complying with all major international standards,
such as API, ISO and DNV. Such pipes are used for lines
that transport oil and gas from Chinese oil rigs in the
north to cities in the east and south of the country.
Messe Düsseldorf GmbH
– Germany
www.messe-duesseldorf.dePhoto credit: copyright H Butting GmbH & Co KG