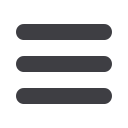

8
J
uly
2010
www.read-tpt.com›
I
ndustry
N
ews
SMS Elotherm has commissioned a new
system to inductively heat large diameter
pipe segments for an Italian pipe bending
facility.
The inductively heated pipes are bent by
the “Hamburg process”. The straight pipe
is inductively preheated and then worked
over a curved mandrel.
A second toroid-shaped induction coil
heats the inner pipe region while the pipe
is bending on the mandrel.
The resulting bent pipe segments
have exceptionally high strength,
qualifying them for critical applications
such as nuclear and combustion power
plants, chemical plants, and oil and gas
pipelines.
The ability to heat large pipes with
diameters up to 1,200mm (4") and wall
thicknesses up to 50mm (2") makes
this a remarkable system. A 2,400kW
straight inductor coil preheats the pipe to
750°C (1,380°F). The 1,600 kW curved
inductor coil brings the tube up the 850°C
(1,560°F) on the bending mandrel.
The working throughput is up to
11,500kg (25,000lb) per hour.
With this induction heater, the customer
that takes advantage of it can make high
quality value-added products for safety
critical applications, helping to advance
its worldwide leadership in the bent pipe
market.
SMS Elotherm
– Germany
Fax: +49 2191 891 726
Email:
info@sms-elotherm.deWebsite:
www.sms-elotherm.deLarge pipe bending system commissioned
TUBE and Pipe capacity in China has
increased fivefold in the past decade, with
China producing nearly half of the world’s
tubular goods.
This segment is a key strategic growth
segment for Quaker. “We draw on our
process expertise, proven solutions, and
technology from around the world to act
as a ‘front-to-back’ supplier of lubricants,
coolants, and cleaners [for the front-end
process], and a complete portfolio of rust
preventives and final coatings at the back
end,” says Karl Kunkel, Quaker’s global
director of strategy.
Currently, Quaker supports many tube
and pipe customers throughout China. In the
north, Quaker supplies a significant amount
of welded pipe forming fluids, threading
and hydrotesting fluids, and UV curable
coatings. In the south, Quaker supplies
water dilutable rust preventives, as well as
threading and hydrotesting fluids. Quaker
is looking to expand into China’s seamless
mills with both QUINTOLUBRIC
®
fire-
resistant hydraulic fluids and customised
hot rolling lubricants.
“We have established ourselves as
a trustworthy and committed partner in
China,” comments Albert Ma, business
director of Quaker Asia Pacific. “We are
targeting growth within additional ERW
forming lines, and UV-curable corrosion
preventives. In particular, UV opportunities
are a perfect fit for Quaker, as they give us
the ability to work closely with customers
on value-added projects – presenting a
true win-win scenario.”
Quaker has experienced great success
in the global process chemical marketplace,
thanks to its mission to ‘Deliver Everywhere
the Best from Anywhere’. Currently, Quaker
China has 10 satellite offices and employs
over 200 people.
Quaker’s Asia/Pacific headquarters
are located in Shanghai, and include
manufacturing, lab facilities (with 30
chemists, supported by Quaker’s global
R&D group), and office personnel.
Throughout 2010, Quaker expects
continued growth and expansion in China,
both internally and in its customer base.
Quaker Chemical
– USA
Fax: +1 610 832 8682
Website:
www.quakerchem.comQuaker Chemical capitalises on product
portfolio in China’s tube and pipe market
SMS has commissioned a system to inductively
heat large diameter pipe segments
Quaker supplies a range of lubricants,
coolants and cleaners