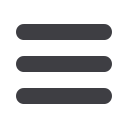

October 2009 Tube Products International
49
Mater ials
Tube and pipe
Hot roll bonding of various steel grades
in itself is not new. However, to date it
has not been used with coil material,
but rather for heavy plates in the
production of corresponding slabs.
The procedure creates a homogenous
metalline bond at the atomic level
between the individual layers in a single
step.
The high adhesive power of this bond
can be evidenced using shear tests,
among other things. As a coil material,
TriBond can be processed economically,
and it can be etched, cold-rolled and
processed like conventional steel
strips.
During production, the preliminary
strips and the appropriately prepared
slabs are first cleaned of any forging
scales, placed on top of each other and
connected with circular welds.
The welds stabilise the steel package
and prevent the intrusion of furnace
atmosphere between the individual
layers during the heating process, which
leads to the creation of forging scales.
The material bond is created when the
steel package, heated to approximately
1,200ºC, is pre-rolled in the roughing
stand of the hot strip mill at a pressure
between 2,000 to 4,000 tons.
Afterwards, the material may be rolled
to hot strips of 2.5 to 7.5mm and cold
strips of 0.1 to 2mm. The selected
thickness ratio of the individual material
layers remains stable during the entire
process.
The composite material can conceivably
be used in automobiles, as a crash
element, for example.
During an axial crash test, a rectangular
TriBond tube with the dimensions of
60mm x 60mm x 350mm and a wall
thickness of 1.13mm was tested.
The C70/C15 test sample made of cold-
rolled, annealed plate, which had been
formed into a tube using a longitudinal
laser weld, showed very even energy
absorption along the path of distortion
and very symmetrical distortion.
Researchers are currently working on the
further exploitation of the potential of the
procedure. For example, asymmetrical
layer designs can be produced, where
layers of varying thickness and strength
enclose a core material that can be
re-formed.
In addition it is possible to combine high
tensile strength and good re-forming
characteristics or to connect wear-
resistant materials with weldable ones.
A further project in development
is Nirosta
®
TriBond as three-layer
combination of high-grade steel
with low carbon ratio with corrosion,
acid and heat resistant steel grades.
Possible uses in this regard are tubes
with corrosion-resistant surfaces for the
chemical industry as an economical
alternative to stainless steel tubes.
New developments in the tube
material sector are a central topic of
the international trade fair, Tube 2010,
which will take place at the Düsseldorf
exhibition grounds from 12 to 16 April
2010. In addition, the trade fair will
again present the entire range, from
tube production and processing to
utilisation. After a successful premiere in
2008, the sections Pipelines and OCTG
Technology will again be showcased.
Information supplied by Messe
Düsseldorf GmbH
ThyssenKrupp Steel AG
– Germany
info@thyssenkrupp.com www.thyssenkrupp.comMesse Düsseldorf GmbH
– Germany
info@messe-duesseldorf.de www.messe-duesseldorf.deThyssenKrupp Steel’s latest developments in tube steel grades involve higher tensile
S
S
materials for standard grades and HIC steel grades
The TriBond crash element shows very
▼
▼
symmetrical distortion after the axial
crash test
Photo credits: ThyssenKrupp Steel