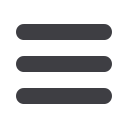

October 2009 Tube Products International
61
after installation. One opening was made in the upper
area of the old pipe both in the starting construction pit
and in the destination construction pit. These openings
allowed the remaining water quantity that was unable to
be discharged by the existing drainage facilities to be
pumped off. High-pressure cleaning was then carried
out immediately, with simultaneous extraction and
transportation away of the sludge residue.
The solid incrustations left behind were removed by
mechanical cleaning. Calibration then provided a
‘surprise’ – unlike the specifications in all planning
documents, the old pipe in the repair section was not
DN 1,050, as assumed, but was only DN 1,000. In
order to able to use the PE 100 pipes already on site,
it was necessary to implement a more major reduction.
The technical parameters were recalculated. The high
flexibility of the Simona PE 100 pipe allowed the work to
continue within tolerance with no interruption.
Calibration with 985mm diameter followed by a
concluding camera inspection ensured that the old pipe
had been adequately prepared for the pull-in operation.
The counter-bearing structures required in the starting
construction pit and destination construction pit were
allowed for as early as digging the construction pits.
The swagelining process met all these requirements.
A great deal of positive experience with preceding
constructionprojects done by LudwigPfeiffer documents
the reliability of this repair process.
The swagelining process
The swagelining process is a cost-effective process
for the repair of discharge pipes comprising standard
PE 100 pipes without permanent annulus. It is one of
the reduction processes in accordance with DVGW
W 320. In the case of the swagelining process a long
pipe train comprising several Simona PE 100 pipes
is prefabricated on the construction site. The outer
diameter of the PE 100 pipe, at 1,060mm, is larger than
the inside diameter of the old pipe in order to guarantee
a durable Close-Fit position after installation.
The cross-section is reduced by tensile force and
compressive force for the duration of pipe pull-in. The
new pipe is pulled in with a pulling device on-site by a
reduction tool. The pipe remains constantly subject to
tensile stress during the pull-in process. Consequently,
it can be interrupted at any time, eg in order to connect
individual pipe trains before the pipe pull-in operation.
When the final position is reached, the tensile force
is reduced, thus increasing the outer diameter again.
The result is a perfect Close-Fit. The new Simona PE
100 pipe tightly follows the course of the old pipe. One
major advantage of this process is that time-intensive
preliminary work, such as cleaning the old pipe and
welding the individual pipe trains, can be carried out in
parallel in the construction process.
Preparatory measures
Various types of preparatory work were required so that
the new pipe could be easily pulled into the old pipe and
so that a Close-Fit position in the old pipe was reached
Figure 2
▼
▼
: Hot-tool butt welding is used to join the two pipe
trains tension-proof with one another
Figure 4
▲
▲
: The complete pipe train was pulled into the existing
pipe in a single pulling operation
Figure 3
▲
▲
: The 500m long pipe train was moved without difficulty
to the starting pit using lightweight equipment