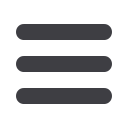

28
Mechanical Technology — April 2015
⎪
Hydraulic and pneumatic systems
⎪
“
C
onnection technology plays
a pivotal role in pneumatic
factory automation. As
with any other technology,
it has evolved and adapted to become
more functional and modular,” says
Schwulst, before listing some of the
trends – good and bad – that he has
observed.
Grey market products
“In South Africa, we are seeing an influx
of low cost fitting and tubing products,”
he says. “Cheaper doesn’t often mean
better, however, and these grey market
How integration is changing the pneumatic valve market
H
ave you ever opened a product
brochure and been overwhelmed by
the sheer number of options? Choice
is great, but past a certain point it leads to
diminishing returns. When it comes to inline
valves, there definitely exists too much of a
good thing.
The good news for anyone who’s ever
been tempted to throw a brochure against
a wall in frustration is that valve trends
are moving towards consolidation without
sacrificing functionality. As the technology
has moved forward, we have seen greater
integration of options. Instead of having
to find the right match from multiple valve
series for your application, all the features
are now incorporated into one series.
This kind of thinking takes a page from
car manufacturers. Instead of each car hav-
ing its own specific part, certain components
are common across a variety of vehicles. This
brings down production costs as manufac-
turers can produce a large volume of a few
components rather than a small volume of
many different parts. The end result is that the
saucy car you have your eye on is much more
affordable than it would’ve been otherwise.
Until now, customers looking for valves
with specific features had to choose between
numerous different series. Our own inline
valves portfolio has included four distinct
series: Tiger Classic, Tiger 2000, Midi and
CPE.
The integration of valve functionality
means that today we can offer a single series
of inline valves that consolidates all of the
benefits and options of the different series.
The tough and robust VS Series streamlines
everything you might need out of a valve
into a single group. It includes features such
as internal or external piloting, mechanical
or pneumatic reset, manual or de-tenting
override and much more. In addition, the
series covers all of the ATEX requirements
and voltages you might need.
This consolidation offers a myriad of
benefits to consumers. The obvious one
is that the choice of valve has never been
easier. Instead of needing to do research
on what valve would suit your functionality
best, customers can quickly find an all-in-
one solution.
Manufacturers are able to take advantage
of the benefits of mass production. A single
series translates into a higher production
volume, which brings production costs
down. Customers can therefore enjoy these
integrated valves at attractive prices.
It’s a fantastic example of how to translate
engineering expertise into something that
reduces unnecessary complexity while in-
creasing quality, efficiency and affordability.
From now on, you’ll barely have to break a
sweat when searching for cost-effective, high
performance valves.
q
Pneumatic connection technology in 2015
Festo South Africa’s business development manager, Russell Schwulst,
discusses the current trends in fittings and tubing – from grey market products
to energy savings that will help to maximise the efficiency of the production
line – the good and the bad of recent trends.
products are having a detrimental impact
on pneumatic systems due to leaks and
shorter lifespans.”
He adds that since no production line
can afford to be idle, quality materials
need to be selected and utilised. “Fittings
and tubing remain major components
at the heart of events, and should be
considered and treated with similar
importance as any module or pneumatic
component.”
Environment- and application-
specific solutions
Schwulst says, “Factories have realised
that not all tubing is created equally. As
such, the suitability of tubing for use in a
specific environment is largely dependent
on the material. Characteristics, such
as flexibility, temperature and media
resistance, are all affected by the mate-
rial used. This is why the proper tubing
needs to be selected for the appropriate
condition and application.”
He adds that an application that uses
UV radiation, for example, will require
different tubing to one that operates
within an environment involving coolants.
“Fortunately, since modularity and variety
are possible, individual solutions can be
tailored to requirements.”
Standards and regulations
“Not only are businesses realising that
fittings and tubing need to be specific
to the environment and application, but
industry standards, testing and regula-
tions are also ensuring they remain top
of mind,” explains Schwulst. “Apart
from guaranteeing the correct material
is being selected and utilised, there is a
health and safety element, too. In a heat-
intensive environment, for example, the
incorrect fitting and tubing combination,
or perhaps even the use of inferior prod-
uct, could cause a pipe to burst or come
lose resulting in an injury to an operator.”
Energy-saving
In the midst of the current national power
crisis, energy saving is vital, he adds.
“Load shedding is becoming inevitable
and factories need to maximise the ef-
ficiency of the production line before the
lights go out and the expensive genera-
tors kick in. Leakage and breaks have a
negative impact on operational costs as
well as energy-efficiency, because they
slow down the rate of production,” he
warns. “By using quality equipment in
the correct application, a business can
lower operational costs, and cause less
strain on the already constricted power
grids,” he says.
q