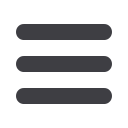

36
MODERN MINING
January 2016
DIAMONDS
Top projects
utilise AG milling, which Petra describes as a
gentler recovery process that breaks down ore
via attrition rather than crushing, and HPGR
technology, which employs inter-particle crush-
ing. The +25 mm material will only be exposed
to AG milling while the -25 mm material will
be liberated through the HPGRs, eliminating
the need for high impact cone crushing.
The plant will also make use of XRF to
replace Dense Media Separation with only
the -12 mm material reporting to the DMS cir-
cuit. The XRF machines are being supplied by
Russia’s Bourevestnik, one of the pioneers in
the XRF field.
While some of the technology being
deployed in the new plant is relatively new to
Southern Africa, it is nevertheless well proven.
Jim Davidson, Petra’s Technical Director, com-
ments: “AG milling is new to South Africa
– and to Petra – but AG mills have been used by
Russia’s Alrosa for many years and their capa-
bility in the processing of kimberlite ore is well
established. In Africa AG mills are installed at
the Catoca mine in Angola and more recently
the technology has been adopted for two dia-
mond projects in Botswana – the new Karowe
mine near Orapa and the Ghaghoo mine in the
Central Kalahari.
“As regards HPGR machines, they were first
introduced at Cullinan more than 15 years ago
– in fact, Cullinan was the first kimberlite mine
to make use of the technology. XRF is also well
proven, both in concentrating and final recov-
ery roles.”
The new plant will be extremely energy effi-
cient – Petra estimates that it will deliver a 12 %
increased energy efficiency per tonne compared
to the existing plant. IE3 Top Premium motors,
enabling an almost constant efficiency in the
75-100 % load range, will be used throughout
the facility while variable speed drives will
drive conveyors and pumps. Motor Control
Centres (MCCs) will be equipped with multi-
step, low voltage power factor correction units,
significantly enhancing the ability to manage
current load, and all lighting will be energy
efficient. In addition, the use of a gravity-feed
slimes disposal system will reduce the need
to pump slimes. Total power con-
sumption will be 25 MW compared
to the 22,5 MW of the existing plant
but the new plant will treat 6 Mt/a
as opposed to the 5,3 Mt/a handled
at present.
Water consumption will also
improve – by a massive 66 %.
Present water consumption is 3,5 m
3
per tonne treated while the new
plant will only require 1,2 m
3
per
tonne treated.
While ‘brownfields’ projects
can sometimes be problematic,
Davidson says that Petra is confi-
dent that construction will proceed
smoothly. “There are integration
Schematic of the new
processing plant.
The existing plant at
Cullinan (seen here) covers
26 ha. It will eventually be
dismantled, removed and
mostly sold for scrap.