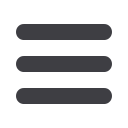

January 2016
MODERN MINING
69
Top projects
COAL
innovation at
Shondoni
The massive winder house
was moved by crane across
58 m and hoisted to a height
of over 30 m before finally
being positioned on top of
the headgear.
technology to inject grouting via pipes inserted
down holes drilled in front of the work area,”
said Louw.
The shaft inclines at 12 degrees for a dis-
tance of 980 m, housing the 3,5 m/s single
incline conveyor that will extract 3 200 tons of
coal per hour.
Coal will be mined mainly from the 4-m
thick Number 4 seam at between 140 m and
160 m below surface, by normal bord-and-
pillar methods as employed at Middelbult.
Continuous miners break the coal and load
into shuttle cars, which deliver into feeder
breakers; an underground crusher sizes the
coal to -150 mm lump size. Section conveyers
take product onto trunk conveyors, which in
turn deposit it into underground bunkers; coal
reports to the incline conveyor from the main
underground bunker on Number 4 seam.
The 15 000-ton capacity surface bunker –
constructed by Stefanutti Stocks Civils – also
adopted an interesting approach by using pre-
cast ‘planks’ up to 20 tons in weight to facilitate
a safe and efficient construction process. Cast
in a dedicated precast yard nearby, the compo-
nents were placed sequentially by gantry crane
and stitched by concreting.
“This innovation led to a substantially safer
working environment, with much less need for
scaffolding and working at height during con-
struction,” said Louw.
The design went on to be commended at
the Concrete Society of Southern Africa’s
Fulton Awards 2015, where it was described
as an excellent example of hybrid or compos-
ite reinforced concrete structures – showing
the benefits of precast combined with in-situ
concrete.
Leading from the bunker is the record-
breaking, 21-km-long conveyor. It is reportedly
the longest in the world that can run this dis-
tance with drives only at the head and tail, an
achievement made possible by a more energy-
efficient drive system that reduces power
consumption.
“It must also curve to avoid a settlement and
a gold mine tailings dam and must cross roads
and waterways,” said Louw. “Environmental
concerns also demand that the belt is spill-free
and must be sealed when it crosses sensitive
areas.”
To minimise the environmental impact
of the conveyor, it was necessary to prevent
carry-back spillage along the conveyor route.
This was addressed by installing belt turn-
overs – at head and tail – to rotate the belt 180
degrees as it turned. This ensures that the dirty
side of the belt is facing up for both top and bot-
tom strands of the conveyor, stopping residual
material from falling off the belt as it passes
over idlers.
The conveyor is covered over its full length
to prevent rain from washing coal dust off the
belts, and to reduce the propagation of dust and
noise; dust suppression sprays at the transfer
chutes also help keep coal dust to a minimum.
The installed drive capacity on the conveyor
is a substantial 5 MW, with four drives at the
head and a single drive at the tail. An 80-ton
counterweight puts the necessary tension on
the belt to prevent slippage at either end. This
element of the project will be one of the last to
be finalised and will be commissioned in the
second half of 2016.
Maintenance and monitoring of this ambi-
tious conveyor design is clearly vital for smooth