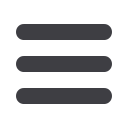

EuroWire – November 2008
43
english technology news
Eurolls’ inline compact stretching unit,
LSO 500, is designed for the production
of high resistant/high yield wire in
accordance with the latest European
standards.
The insertion of this unit into an existing
production line, to produce cross wires in
mesh line or longitudinal wires in lattice
girder lines for example, permits inline
production of high resistant/high yield
wire, ready to be successively processed
into its final welded or bent format.
Eurolls – Italy
Fax
: +39 0432 79650 1821
:
info@eurolls.comWebsite
:
www.eurolls.comTechnical specifications
Type of entry
material
Low carbon
ribbed rod (C =
0.20% C max) with
UTS ≤ 500 N/mm²
Inlet wire rod
diameter
Diameter 5.5mm
to diameter
10mm
Finished wire
Ribbed stretched
Working Coil
Weight
0.8 t/h – 3.3 t/h
Working speed Max 6 m/sec
Inline stretching unit
Inline compact stretching unit from Eurolls
▲
▲
Stefana SpA, a manufacturer of bars
and wire rod, awarded a contract to
SMS Meer in 2005 for the supply and
installation of a complete bar mill for
120 t/h (140 t/h with hot charge).
The objective of the project, named
“Dream Steel” was to significantly boost
production of straight bars and spools.
With an annual capacity of 700,000t,
this new plant has one of the highest
productivities in southern Europe.
The product mix of the bar mill includes
rebars and plain rounds with diameters
from 8 to 16mm produced with the
two-slit rolling method, and with
diameters from 18 to 40mm produced
in a single line.
The SMS Meer scope of supply included
a walking-hearth furnace, the rolling
line, the finishing section and two VCC®
(Vertical Compact Coiling) lines. The
walking-hearth furnace is designed
for heating 160 x 160mm square
billets with lengths of 16 m. With its
dimensions, this unit ranks among the
world’s largest for reheating of starting
material for long-product rolling mills.
When planning the layout of the mill,
space was allowed for the installation
of a billet welder for endless rolling
operation and a possible expansion for
the production of wire rod.
SMS Meer acted as system integrator,
supplying all the electrical and
electronic equipment, controls and
software for the mill automation.
SMS Meer – Germany
Fax
: +49 211 881 4386
:
thilo.sagermann@sms-group.comSuccessful start-up of ‘Dream Steel’ rolling
mill for rebars and plain rounds