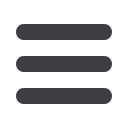

PRODUCT News
56
MODERN MINING
July 2017
Index to advertisers
Allied Crane Hire
31
Babcock
27-30
Booyco Electronics
43
Brelko
17
ContiTech South Africa
2
Discovery Drilling
OBC
Discovery Drilling
38
DRA Projects SA
34-35
Flexicon Africa
11
FLSmidth
25
Komatsu
IBC
Metso Minerals
48
MMD Mineral Sizing
IFC
Mynbou Rigs Africa (Belaz Africa)
53
Powerbit Rocktools
13
Sandvik Mining & Rock Technology
OFC
Specialised Exhibitions
55
Stefanutti Stocks Mining Services
51
Tega Industries SA
7
thyssenkrupp
46
Transcor
10
Weba Chute Systems
49
Winder Controls
9
WorleyParsons
20
Zest WEG Group
15
HPE Africa has delivered 21 new Hyundai
wheel loaders to a leading electricity gen-
erating parastatal in South Africa during
the first half of 2017.
“Robust Hyundai HL770-9S wheel load-
ers, designed for maximum performance
and optimum productivity, offer precise
operation and easy control, even in dif-
Parastatal takes delivery of 21 Hyundai wheel loaders
ficult conditions,” states Alex Ackron, MD
of HPE Africa, the exclusive distributors in
Southern Africa for Hyundai Construction
Equipment. “These versatile machines,
with an operating weight of 22 500 kg and
heaped coal bucket capacity of 6,2 m³, are
perfectly suited to the arduous terrain and
handling requirements at power stations.”
New features of these wheel loaders
include an advanced load sensing hydrau-
lic system with efficient variable volume
pump technology, automatic power shift
transmission with variable shift control
and a multi-stage clutch cut-off feature.
The fully automatic transmission sys-
tem allows the operator to customise
automatic transmission shift timing and
clutch cut-off, based on operating condi-
tions and personal preference. Variable
operating modes – power, standard and
economy modes – contribute to improved
The Hyundai HL770-9S wheel loaders are well
suited to the arduous terrain and handling
requirements at power stations.
productivity, reduced fuel consumption
and enhanced operator comfort.
The combination of high pressure com-
mon rail system and advanced in cylinder
combustion technology in the eco-friendly
Cummins 3 tier engines results in increased
power, improved transient response and
reduced fuel consumption.
The ‘ride control system’ – an optional
feature – has a shock absorbing accumulator
that cushions the boom, reduces material
loss and improves operator comfort.
Hyundai’s new Hi-mate remote man-
agement system enables users to track
and monitor a machine’s performance
and daily operation history. This system
utilises GPS satellite-based technology to
access accurate diagnostic information,
evaluate equipment reliability and verify a
machine’s location.
HPE Africa, tel (+27 11) 397-4670
Sudor Coal implements Booyco proximity detection system
Mpumalanga miner Sudor Coal has
implemented a state-of-the-art proximity
detection system (PDS) from market leader
Booyco Electronics at its Weltevreden
operation.
The underground coal mine near
Emalahleni has three sections extracting
the Number 4 Seam at about 60 m below
surface. The Booyco PDS system includes
buzzers and flash units on mine personnel,
as well as transmitters on continuous min-
ers, shuttle cars and roof-bolters.
The system prevents dangerous situ-
ations by alerting both the pedestrian
and the machine operator to each other’s
proximity; an audible and visual alarm is
triggered followed by retardation of the
moving equipment, which is then brought
to a standstill if no action is taken.
Petrus Vilakazi, underground engineer
atWeltevreden, says the implementation of
the system began in March 2016 and was
rolled out across all three of the mine’s sec-
tions over a period of about a year.
“We initially presented our imple-
mentation plan for a collision-avoidance
system (CAS) to the Principal Inspector at
the Department of Mineral Resources,” says
Vilakazi,“and this year wewere able to report
back to say the system was in place, in com-
pliance with the new safety legislation.”
He says that commissioning of the PDS
was done in two phases. Firstly, there was
a cold commissioning phase in which the
warning systemwas activated. This was fol-
lowed by hot commissioning, in which an
actual intervention – the retardation and
the stopping of moving machinery – will
be triggered if the warning signals are not
heeded for any reason.
Vilakazi says a vital part of the system’s
effectiveness is the buy-in of employees; it
was therefore important to communicate
the rationale for the PDS clearly with the
underground employees to ensure that
everyone understood why it was necessary
and how it would improve safety.
“Anything new takes some time getting
used to, but it was not long before the sys-
tem was well accepted by all stakeholders
and it now works smoothly with no impact
on production levels,” he says. “Employees
also realised that the company had
invested substantially in this system so that
they could work more safely, and they have
bought into the implementation process.”
Anton Lourens, Booyco Electronics, tel 0861 266926