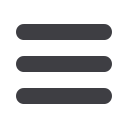

developments
products &
www.read-tpi.comJuly 2009 Tube Products International
33
and qualities of structural hollow steel
sections, both in its delivery and its
long-term performance. Twelve circular
hollow sections supplied by Corus Tubes
wind around the outside of the structure
to create the signature corkscrew-like
appearance, with the slender lines of the
curved steel tubes and the neat welded
joints ensuring the sharp lines of the
structure’s design could be achieved.
The elliptical structure provides an
enclosed crossing, which is fully glazed
with polycarbonate panels, ensuring
a safe and comfortable environment
for pedestrians and cyclists using the
bridge.
All the steel components were subject
to a rigorous testing regime, first by
Corus Tubes during manufacture of the
steel sections at its Corby mill, then by
SH Structures.
SH Structures, used to working on com-
plex tubular steelwork, pre-fabricated
the sections at the company’s facility.
As well as reducing the amount of work
that actually took place on-site, off-site
fabrication of the sections in the closed
factory environment meant work was
unhindered by prevailing bad weather
conditions that might have otherwise
caused delays on the exposed site.
The relatively low weight of the structural
steel components enabled sections to
be easily transported to the site, where
the only work required was the welding
of the splices to create the complete
90-metre span.
TimBurtonof SHStructures commented,
“
The complex design and fabrication of
the bridge meant that the footbridge
components needed to be carefully
pieced together – an intricate process
that was facilitated by the unique
properties of steel which allowed it
to be easily bent and shaped. This
enabled it to be designed to a range
of shapes that were easy to construct,
essentially giving the architect greater
design scope. In addition, the off-
site fabrication associated with steel
ensured that delivery of the project
incurred minimal disruption on the
locality through road closures – which in
itself created significant economic and
health and safety benefits.”
Raynesway Construction carried out the
complex operation to install the main
superstructure section of the footbridge
using one of the UK’s largest cranes,
complete with a 90-metre job and 600
tonnes of superlift counterweight.
The crane itself took a week to
assemble, having been delivered to site
in 45 separate loads. However, once
erected it was able to lift the 230 tonne
superstructure element of the footbridge
into position using a single operation
that commenced at 8.30pm.
Once the new bridge was successfully
located and secured into the support
structure, the lifting slings attaching the
bridge to the crane were removed and
the motorway was re-opened at 3am
the following morning – some three
hours earlier than planned – ensuring
that closure of the motorway was limited
to one evening.
Corus Tubes
– UK
www.corustubes.co.ukThe bridge was lifted into place in one
▼
▼
night