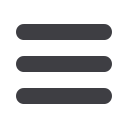

Connectors
Fi t t ings , Flanges &
44
Tube Products International July 2009
www.read-tpi.comDhatec has been working on an R&D
programme for the past five years,
focussing on how to keep line pipes
in optimal condition during and after
manufacturing.
During each segment of the logistic trail,
there is a risk of damaging both the
pipe and its coating layer. As a result of
the R&D programme, present problems
are isolated and professional solutions
are found. In many cases these new
solutions do not only safeguard the
quality of the pipe and coating, but also
improve the process itself in terms of
efficiency and safety.
One of the new developments is the
Premium Pipe Coupling. A coupling lines
up pipes and protects the bevelled pipe-
end during external coating. This allows
coating plants to achieve the optimal
end quality of the coating application
and enhances stability and efficiency of
the coating process.
During research on the issues that
pipe coating companies worldwide are
dealing with, it became clear that there
was a need for a professional coupling.
Line pipes are seldom straight or exactly
round. Many coating plants deal with
stability problems during the process or
air seals underneath the coating layer
as a result of radial pipe movement.
Even severe variations in FBE coating
thickness occur because the distance
from the pipe to the spraying nozzle
in the coating cabin varies due to pipe
movements.
Each coating process is different and
experience and fine-tuning are needed
to achieve the best results. However, in
many cases results canbe improved if the
right coupling is applied. By connecting
pipes with a coupling, the distance
between the coating cabin and the first
pipe supporting roll afterwards can be
increased. Directly after the cabin, the
freshly applied coating is still weak due
to the high temperature. Each time the
pipe weld, spirally or longitudinally, of
the rotating pipe hits the first support
roll, the coating can dent or damage.
By increasing the distance, the coating
is allowed to cool down more before
hitting the first support roll, avoiding
loss in quality.
Secondly, by using a coupling, radial
movement of pipes when the weld
hits the support roll, is reduced. An
equally spread coating application free
of air voids is ensured. Normally this is
achieved by lowering the line speed, but
a coupling also solves the problem and
production can run at full capacity.
Dhatec has developed three main
models: Standard Coupling, Advanced
Coupling and Premium Coupling. The
basic demands for the design were:
reducing radial pipe movements to
almost zero; strong, shock-resistant
construction; adjustable for a wide
wall thickness range; bridge thermal
expansion of the pipe in an induction
oven (220°C); small contact surface
with the pipe, to minimise heat loss;
room for cooling water to flow through
the pipe; and fast and easy application
or removal.
An important feature is that the coupling
is placed in only one pipe-end. This
Advanced pipe couplings
Stainless steel fittings and flanges
from Malaysia and China
Steel-Tech Industry Co is a
manufacturer and exporter
of a wide range of stainless
steel products for fittings,
valves, flanges, tubes and
pipes for a variety of industry
applications. The products
are used in industries such
as petroleum, chemical,
machinery, electric power,
pharmacy, papermaking, palm
oil, automobile, oil and gas,
and food processing.
The company has two manufacturing plants, located in Malaysia and China, and
has been certified by DQS ISO9001:2008. The company’s continuous product
development and production quality control is exercised by its technical control
department, which strictly controls raw material selection, production and
inspection.
Steel-Tech Industry Co, Ltd
– Malaysia
stind@pd.jaring.my•
www.stindustry.comFittings from Steel-Tech Industry Co
S
S
Dhatec’s Task Environment, the logistic process of a line pipe
S
S
The Standard Coupling during coating
S
S